Engineered
APPEARANCE CHARACTERISTICS OF ENGINEERED FLOORS
With higher density backsawn hardwoods that are installed in moderate to more humid localities there are concerns with peaking in the floor. This produces a pressure related cupped appearance in a floor that often needs to be sanded out to achieve a flat floor or if more severe has in some instances resulted in the floor being replaced. Following research it is considered that the common 80 x 19mm and 130 x 19mm profiles as outlined in AS 2796 Timber – Hardwood – Sawn and milled products can be redesigned to make the floor less prone to peaking under expansion pressure.
Note that this information sheet has been developed for consideration by flooring manufacturers of higher density timbers mainly in Queensland and New South Wales.
GRAIN, FIGURE AND TEXTURE
As well as a subtle blend of colours, the warmth and inherent beauty of timber is largely contributed to by a combination of grain, figure and texture. With smooth surfaced boards, grain and figure, which are the shapes and patterns evident on the board surface, are clearly visible. Factory processes enable textured surfaces to be created with the board surface being wire brushed prior to coating.
This added texture can range from a mild effect, to more intense. The textured surface also enables attractive different coloured highlights to be created, that follow the figure and grain pattern in the board. When flooring is more heavily textured, care is needed with cleaning.
Damp mopping that is too frequent, or if too much water is used with incorrect cleaning detergent, then these practices can trap dirt in the textured grain. Particularly for textured flooring, ‘dry’ cleaning processes such as an antistatic mop and spot cleaning of more stubborn marks should predominate. Another consideration is that grain running at a shallow angle at some board edges can be prone to some minor chipping. Such chips should be removed and then if desired can be filled with coloured wax, that is made for floor repairs.
BOARDS WITH AND WITHOUT BEVELLED EDGES AND ENDS
Engineered flooring is available in a wide range of board widths and lengths and includes some very wide boards more than 300mm in width, but more commonly in the range from 130mm to 220mm. Engineered flooring is available as planks as well as parquetry, which has notably shorter and often more narrow widths. Parquetry is also available as a standard herringbone block or a chevron cut, which has angled ends.
Some flooring has bevelled edges and ends providing greater board definition in the floor, others with what is termed a smaller micro bevel and then there are other products that are flush at edges and ends. Some minor lipping at board edges and ends can occur but is not considered to be of concern if less than 0.2mm in products without a bevel and with bevels a greater tolerance at 0.5mm is acceptable.
SEASONAL MOVEMENT IN FLOATING FLOORS
Engineered, bamboo and laminate flooring are all products that may be floated on an underlay over a structural subfloor. With floating floors, the boards are fixed to each other but not to the subfloor. Another commonality with these products is that they all contain cellulose fibre which has the property of being hygroscopic.
A hygroscopic material is one that will absorb moisture from the air under higher relative humidity conditions and swell, and under drier conditions with lower air relative humidity, the material will release moisture to the air and shrink. Due to this each of these products used in floating floors are prone to seasonal swelling and shrinkage and as these products are not fixed to their subfloors, seasonal movement effects can be greater at times than some owners or contractors might expect. This information sheet will discuss this aspect of the seasonal movement in floating floor products.
MOVEMENT IN SOLID TIMBER
Firstly, we need to consider solid timber flooring and how it shrinks and swells with changing relative humidity. This is shown in the adjacent diagram with board expansion occurring under higher humidity conditions and board shrinkage under lower humidity condition. Although both temperature and humidity alter throughout the day and night, a floor’s response is usually relatively slow, and we often only see minor changes from month to month. However, during prolonged specific wet periods or consistent hot and dry weather things can be different, and a floor may react significantly over the space of a week. It is therefore necessary that every site and the expected in-service environment is assessed for a floor to be able to perform to its optimum and this includes floating floors, engineered, bamboo and laminate.
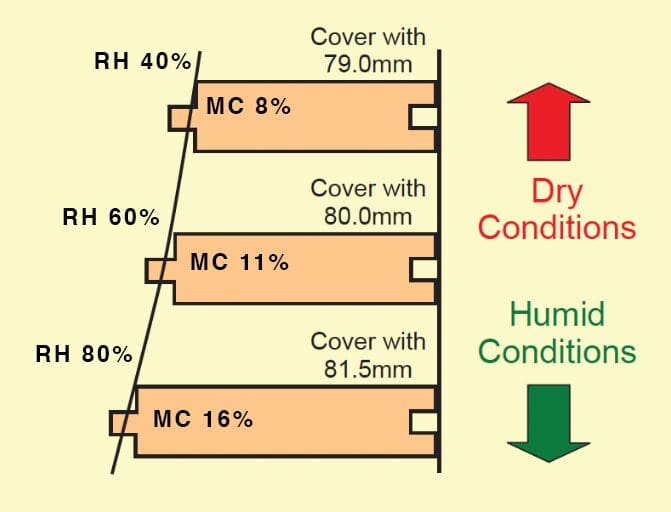
The relationship between relative humidity (RH), moisture content (MC) and board width.
MOVEMENT IN FLOATED ENGINEERED FLOORS
Engineered flooring differs from solid timber flooring in that it is a generally a multi-layered timber product and the reason for this type of construction is that it reduces the amount of width movement in a board when the moisture content of the flooring changes. Hence, under wet conditions an engineered floor will expand but less than a solid timber floor and similarly under dry conditions it will shrink, but also less than solid timber flooring. Movement is mainly in width but there is also some lengthwise movement, and in this respect, it differs from solid timber flooring.
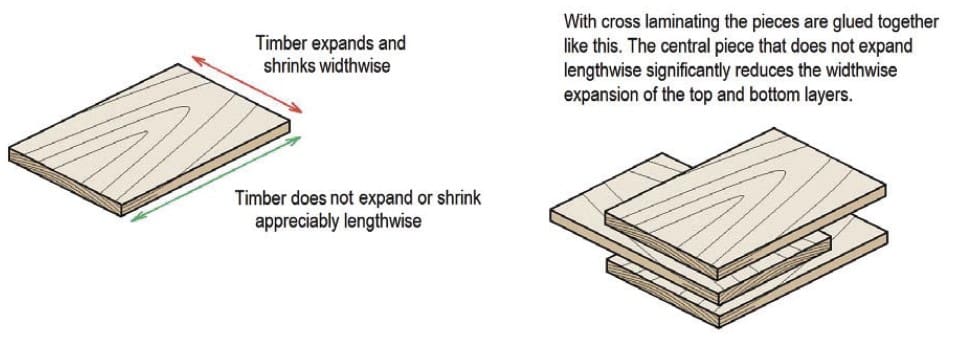
MOVEMENT IN FLOATED BAMBOO FLOORS
Technically bamboo is not a timber but a grass. The most common form of bamboo flooring is strand woven bamboo and to manufacture this flooring, the bamboo is cut into long strands, the strands are then coated with adhesive and under pressure and heat the adhesive cures and a beam is formed. The beam is then cut into boards. The fibres generally align and due to this, most of the movement with changes in humidity is in the width of board, but we do get some lengthwise movement as well. With floated floors the seasonal movement in board width (shrinkage and swelling) is usually more than with engineered and laminate floated floors.
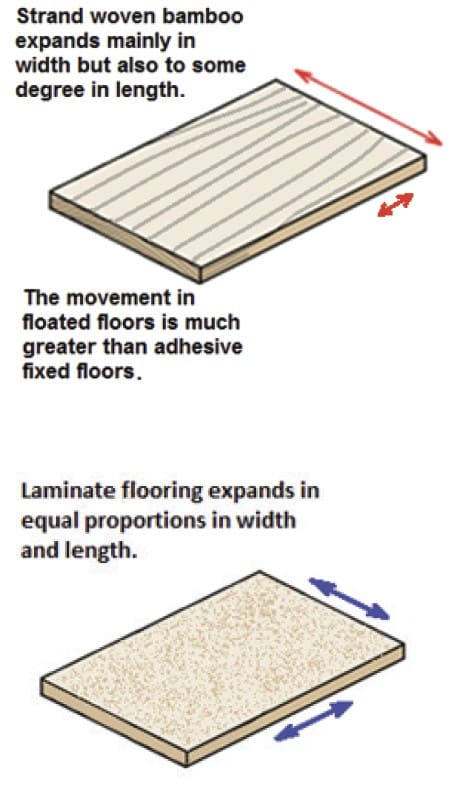
MOVEMENT IN FLOATED LAMINATE FLOORS
Laminate flooring differs from the above two types in that the core layer is high-density fibreboard. In fibreboard the wood fibres are not orientated in any particular direction. The seasonal movement is therefore equal in both the width and length directions. It is important to understand this difference in the above two products.
RESTRICTIONS TO FLOATED FLOOR MOVEMENT
Traditionally, flooring was held in place by nailing it to the subfloor surface. Floating a floor is an installation system which originated in Sweden in the late 1970s with the development of Pergo, a reinforced laminate flooring product.
The term ‘floating floor’ actually describes the method of installing the flooring product, not the product itself. Floating floors are not fixed to the subfloor, with most products having an interlocking, glue-less joining system, although some, with a tongue and groove profile, use adhesive between board joints to hold boards, one to another. A floating floor is sequentially installed over a foam underlay to create a floor “raft” that is able to “float” on the underlay. The benefits of a floating floor include easy laying, a cost effective installation, engineered durability and the flexibility to endure expansion and contraction caused by environmental conditions.
RESTRICTIONS TO FLOATED FLOOR MOVEMENT
Some installers are not complying to the basic rules for the installation of floating floors. That is, kitchen benches and the like are not to be placed on a floated floor, sealant is not be used where the floor meets vertical surfaces (e.g. at benches and skirting), and the installation of control joints at doorways and in hallways should not be left out, due to either the contractor or homeowner considering them to be aesthetically displeasing. If one area of the expansion zone is compromised, this can cause the floor not to ‘float’ as it should and eventually cause the flooring to buckle or separate. If the floor does buckle, or experience excessive movement, and the manufacturer instructions have not been followed, then it is likely any manufacturer warranties on the flooring would become void, and the cost of fixing these often borne by the contractor who installed the floor.
It should be noted that in addition to kitchen benches, other heavy furniture items may also be unsuitable for floated floor installations, such as pool tables, although this does not include items such and beds, most lounge furniture and kitchen appliances. Waterfall benchtops have become popular in recent times, and this is where the benchtop surface cascades down one or both ends of the benchtop, to the floor, but should not be resting on top of the floor.
Being a ‘wet’ area, some contractors are using silicone to create a neat and tidy finish to the waterfall, and this has also resulted in problems due to the restriction it places on floor movement. The photo to the right, depicts one such case where there were concerns with vertical movement adjacent to the bench as the waterfall was resting on the floor, and also the use of silicone between the bottom edges of the benchtops and the floor was providing further restriction to floor movement.
Cork tile installation
Cork is a durable and natural material with unique properties that make it desirable for flooring. The nature of cork (the bark of a tree) is that it has many enclosed air cells and contains the substance suberin that naturally repells moisture. Due to its structure, it has sound deadening properties, provides thermal insulation and objects are less likely to break if dropped on the floor. Similar to wooden floors it is suited to those with allegies and a coated floor is resistant to effects to water on it, much moreso than a wooden floor.
This information sheet will outline installation methods for cork tiles, noting that there are a wide range of products available including some that have a coloured surface.
More traditional cork tiles are sanded and coated simlar to timber floors, although techniques differ, and the sanding and coating of these is discussed in ATFA information sheet 74 Sanding Cork Floors.
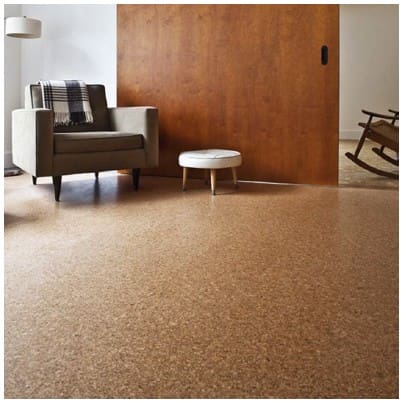
PRODUCT TYPES
The more traditional cork tiles, destined for sanding and coating generally come in a tile size of 305 x 305mm or 300 x 300mm and a thickness of 6mm. Such tiles are adhesive fixed to the subfloor and then sanded and coated. As such the natural cork colour tones are present in the finished floor.
The density of cork can vary between products and generally the higher density cork is seen as being the more durale product with better recovery from longer term marks of furniture legs etc. Medium density cork would be considered to be 400 to 450 kg/m3, while high density cork would be about 500 kg/m3.
More recently, square and bevel edged prefinished cork tiles have entered the market. With these tiles not only can the colour tones be darkened, but the tile can be made with a coloured surface. The tiles are factory clear coated and a further clear coat of the desired sheen is applied after installation, which assists in sealing the joins. Note that these products are commonly installed using a contact adhesive. The underside of the tile is coated with adhesive (this more often by the manufacturer/supplier) with the same adhesive applied to the subfloor.
Cork ‘planks’ are also available and are more akin to a ‘click’ together engineered or laminate floor, with a thin layer of coloured cork, often about 3mm thick, bonded on to high density fibre-board and bonded cork underlay beneath. The planks, that may be 900mm long and 300mm wide are then laid as a floating floor.
As these last two product types are proprietary, the manufacturers will have specific instructions that need to be followed and the focus of this information sheet is on the traditional product that is site sanded and coated.
INSTALLATION OF TRADITIONAL ADHEISVE COATED CORK TILES, FOR SANDING AND COATING.
Although some cork products are designed for the DIY market, such products can also be profressionally installed. If the tiles are to be sanded and coated then it is recommended that a flooring contractor with suitable experience in cork be engaged.
SUBFLOORS
Cork tiles are directly adhesive fixed to the subfloor and are able to be installed on suitably prepared sheet subfloors of plywood or particleboard, and concrete slabs. If the flooring is to be installed over a strip timber floor, or sheet flooring in poor condition, then a masonite underlay that is secured first, may be used. Also if laying over a timber strip floor, that floor should have top nailing repunched and all timber floors acting as the subfloor rough sanded.
It is particularly important that the subfloor is flat, clean and smooth to avoid poor adhesion or imperfections that will telegraph through and show in the cork surface. Subfloor flatness should not exceed 3mm variance under a 3m straight edge, with the straightedge resting anywhere on the subfloor.
Cork is generally adhered to the subfloor with water-based contact adhesives. These adhesives are sensitive to alkali salts in concrete and if they rise to the surface they can cause tiles to lift. Due to this, all flooring direct to slabs should be tested for moisture and to have a surface alkalinity of less than a pH of 10. The test provisions for slab moisture and alkalinty as outlined In AS 1884 – Resilient Sheet and Tile Floor Covering may be used. Note that greater care is needed with on-ground slabs with it often necessary to include an applied moisture vapour barrier to manage possible moisture vapour transmission, and with the concrete slab not subject to hydrostatic pressure.
Prior to laying thoroughly clean the subfloor by vacuum cleaner.