When laying timber floors in older dwellings, as part of renovation work or repairs, there are two buildings products that require our special consideration. These are asbestos in terms of health concerns and magnesite which can affect both our health and building integrity. This information sheet will discuss aspects relating to each that the flooring contractor needs to be aware of when undertaking work in older dwellings. Initially we will discuss asbestos and secondly magnesite.
Asbestos
To a degree we all are likely to have some understanding of the negative and dangerous effects of asbestos, as information about it has been in the news for some years, and the building trades also dealing with it over the years. However, as we do not generally come across it on a daily basis, the details of what we need to consider are not always at our fingertips. This information sheet is therefore not intended to be comprehensive but to provide a refresher on some of the important aspects that we should be aware of.
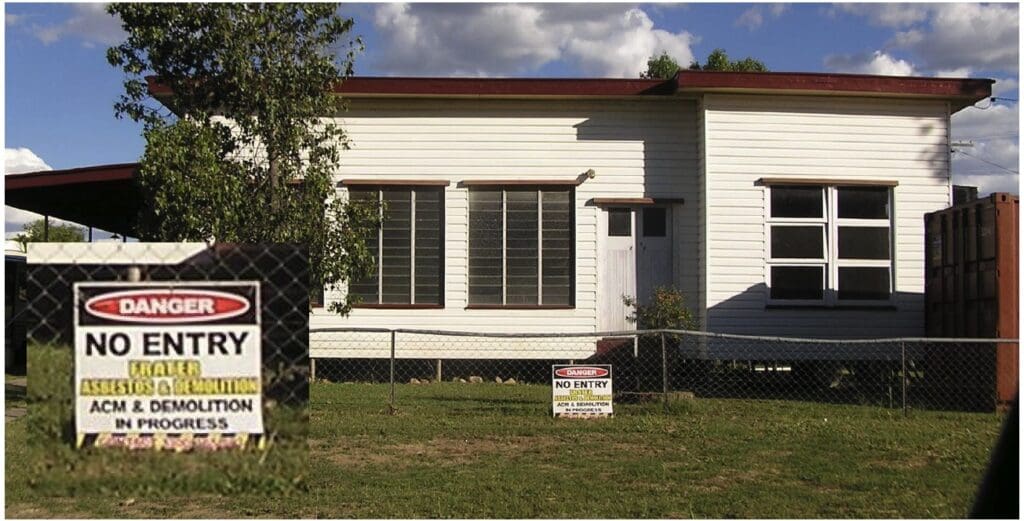
A house closed off for asbestos removal after flood inundation and prior to floor repair
Asbestos was present in many products (about 3000) including building products such as vinyl flooring, wall linings and magnesite. Dwellings built prior to 1987 are likely to contain asbestos and it came in two forms, friable and non-friable. The form of most concern is the friable, which can contain up to 100% asbestos, was present mainly as a soft or crumbly material and was used in fireproofing, soundproofing and ceiling insulation. Non-friable or bonded asbestos is generally rigid with an asbestos component typically less than 15%, and it is less dangerous. However, non-friable asbestos was also used in backing and adhesives for vinyl floor tiles. Renovation work now posses the greater risk to asbestos exposure and one study in Australia reported that 61% or DIY renovators reported being exposed to asbestos and of these 58% indicated that they had cut asbestos.
Of great assistance to us is the Asbestos Awareness website. It not only provides information on asbestos but also factsheets and checklists at https://asbestosawareness.com.au/fact-sheets/ .
Asbestos
To a degree we all are likely to have some understanding of the negative and dangerous effects of asbestos, as information about it has been in the news for some years, and the building trades also dealing with it over the years. However, as we do not generally come across it on a daily basis, the details of what we need to consider are not always at our fingertips. This information sheet is therefore not intended to be comprehensive but to provide a refresher on some of the important aspects that we should be aware of.
On this website there is a specific downloadable check sheet relating to ‘Layers of Floor Covering & Floor Sanders (stripping carpets)’, the front page of which is shown.
Briefly, in terms of encountering asbestos or possible asbestos on site the following should be noted when working on older buildings:
- If you suspect a product could have asbestos, then find out or assume it does and get it tested. Do not disturb it in any way as doing so can release the dangerous fibres.
- From a flooring perspective pre-1987 products of concern include vinyl and lino flooring, adhesive used with these products and with carpets, fibrous carpet underlays and some others, magnesite underlayment and some fire-retardant board materials placed in front of fireplaces or material used in door jambs for fire doors.
- Only qualified tradespeople with asbestos awareness training can work on materials identified as asbestos.
- Licensed asbestos removalists are required with some forms of asbestos removal and when the quantity to be removed is larger. All friable asbestos must be removed by a Class A licenced asbestos removalist. There are legal requirements over asbestos removal and disposal.
- Asbestos, if undisturbed or covered over can usually remain in a dwelling.
- Appropriate protection is needed when working around asbestos products and such products should not be cut, drilled, cleaned, sanded or sawn etc.
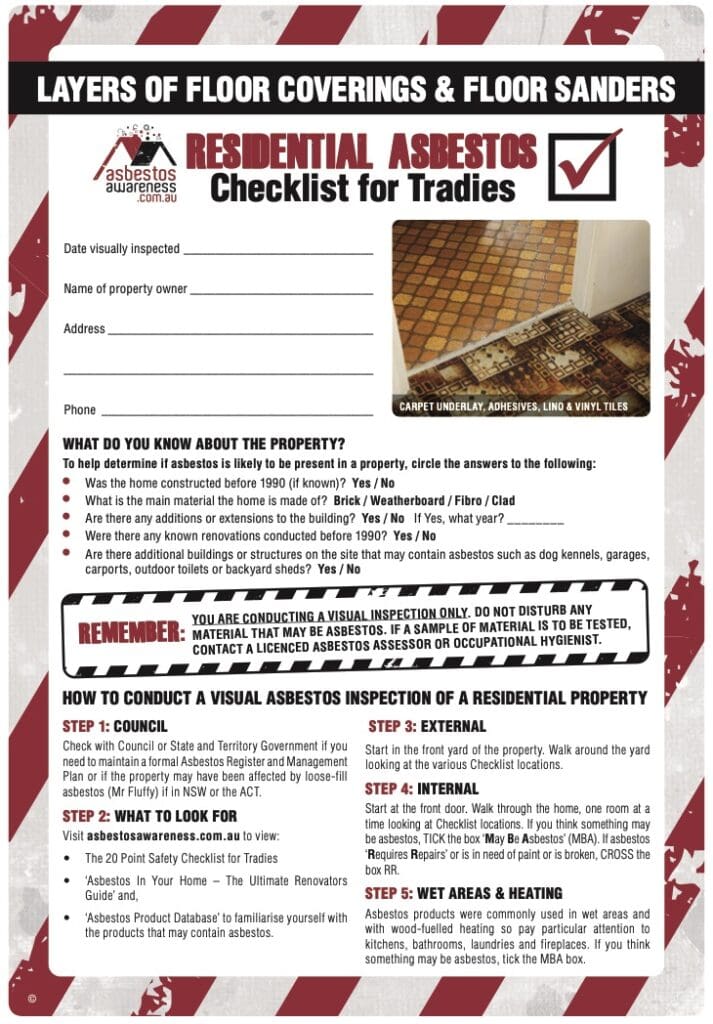
Asbestos Awareness check sheet for flooring
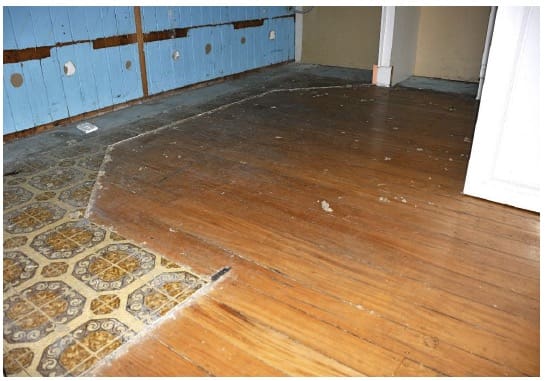
Floor tiles likely containing asbestos
Magnesite
Magnesite was commonly used in the late 1960’s and 70’s and more so in some locations such as Sydney. Its prime purpose was as a levelling underlayment that would also provide sound deadening in unit and apartment developments. To manufacture it, a magnesium chloride solution was mixed with magnesium hydroxide powder, which would then react to form a cement type binder. This is combined with a filler material to achieve the final product, with the filler being either sawdust, cork, wood fibre or asbestos. As such it would be applied as a cementitious topping to create a floor surface often about 25mm thick and with carpet and vinyl often laid on it. These days the flooring contractor is more likely to come across magnesite over concrete slabs in older high-rise apartments.
Other than the possibility of it containing asbestos, time has exposed a number of other problems with it. It is both hygroscopic and moisture sensitive, thereby affected by any sort of wetting (including cleaning water) and this has resulted in the wood fillers decaying, the magnesite breaking down if remaining wet, and resulting in unpleasant odours.
However, another serious concern is that the chlorides present can leach, or breakdown of the product can release chlorides and cause attack of the concrete, reinforcing and any fixings. This being a form of ‘concrete cancer’ and often resulting in significant building repair costs.
Due to the above concerns, it is not recommended that timber flooring be laid over magnesite. This is also line with manufactures of levelling compounds and moisture barriers not warranting their products over magnesite. With on-ground installations, it also needs to be considered that moisture barriers used in conjunction with floated flooring products could exacerbate problems. The moisture barrier preventing the magnesite from breathing and thereby increasing moisture contents at the magnesite concrete level. Hence, even floating floors could exacerbate building problems.
As such, when magnesite is encountered, it firstly needs to be considered that it could contain asbestos and this needs to be dealt with as outlined in the Asbestos section above. Following this the magnesite should be removed.
Any damage caused by the magnesite then needs to be assessed and this likely involving engineers to assess degrade of the concrete and steel reinforcement. The slab is then repaired and assessed for moisture and associated factors when laying a timber floor. Due to the age of the building, and now a bare slab, application of a levelling compound will likely be necessary to meet current flooring installation requirements.
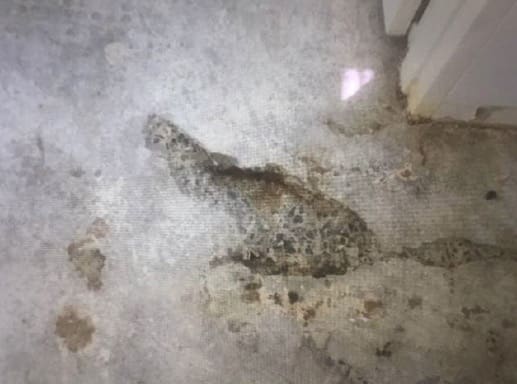
A slab following magnesite removal
Summary
Here we have considered two building products from the past, asbestos and magnesite, both of which have consequences for us today. Their effects were not known at the time of being introduced. However, it is a case of managing health and building effects as applicable, under guidelines that are clearly set out to be followed, before floors can be worked on or laid.