Safety Data and Labelling
Background and Introduction
Hazardous chemicals may be present in products and must be used safely in the work place. It is aimed to achieve this through workers having both knowledge of the hazards they pose and the means of handling these products safely. Employers are responsible for ensuring that workers are provided with the necessary information and training.
In workplaces, relevant information regarding hazardous chemicals should be both on the product label and in the product MSDS, (Material Safety Data Sheet) or SDS (Safety Data Sheet), which must fully comply with jurisdictional legislation. (Note that labels, MSDSs and SDSs from overseas manufacturers may not comply within a country’s specific legislation.)
Most countries are adopting the ‘Globally Harmonised System of Classification and Labelling of Chemicals (GHS)’.
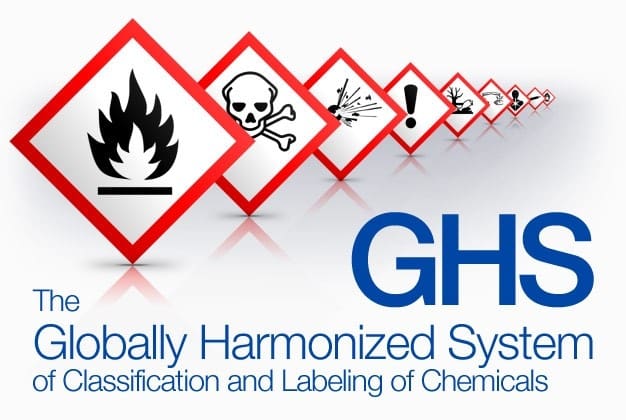
There is a phasing in period currently in progress but this will become a requirement as of 1st January 2017 (i.e. after 31st December 2016).
Compliance will require changes to product labels and the MSDS will be phased out in favour of a SDS (Safety Data Sheet).
‘GHS’ provides for international uniformity of classifying hazardous chemicals and warnings but the ideal of it making overseas product labels and SDS’s compliant in a jurisdiction aren’t necessarily always achieved. There are countries which have not yet adopted GHS classification and also there are some uniquely country specific requirements which remain.
This is especially relevant to products which are imported and may have an SDS prepared by an overseas manufacturer or supplier. Such overseas SDS’s are only acceptable if prepared in accordance with WHS Regulations for that country. If the overseas SDS for an imported product does not comply with the requirements of the WHS Regulations the importer will be responsible for preparing an SDS that does comply.
There are many fully imported, hazardous products used in our industry and unfortunately, we are aware that some importers do not supply country specific WHS compliant MSDS’s or SDS’s. We note also that the importer is responsible for ensuring the chemical constituents of the product are registered within a country, for example, theAustralian Inventory of Chemical Substances (AICS) via NICNAS (National Industrial Chemical Notification and Assessment Scheme).
IT IS IMPORTANT to note that legislation has been changed to make the employer totally responsible for the safety information supplied to his employees (in most cases this will be the contractor or subcontractor). It is no longer a defence to say that it was the manufacturer, importer or supplier who provided you with the SDS or MSDS etc. The employer must seek the appropriate assurances.
If you believe that the MSDS or SDS you have been provided does not comply, in the first instance you should seek advice from your State or Country ‘Work Cover’ or ‘Work Safe’ authority, or equivalent. You may also need to engage an Occupational Health & Safety consultant to confirm or otherwise.
You can also write to the manufacturer or importer using this template:
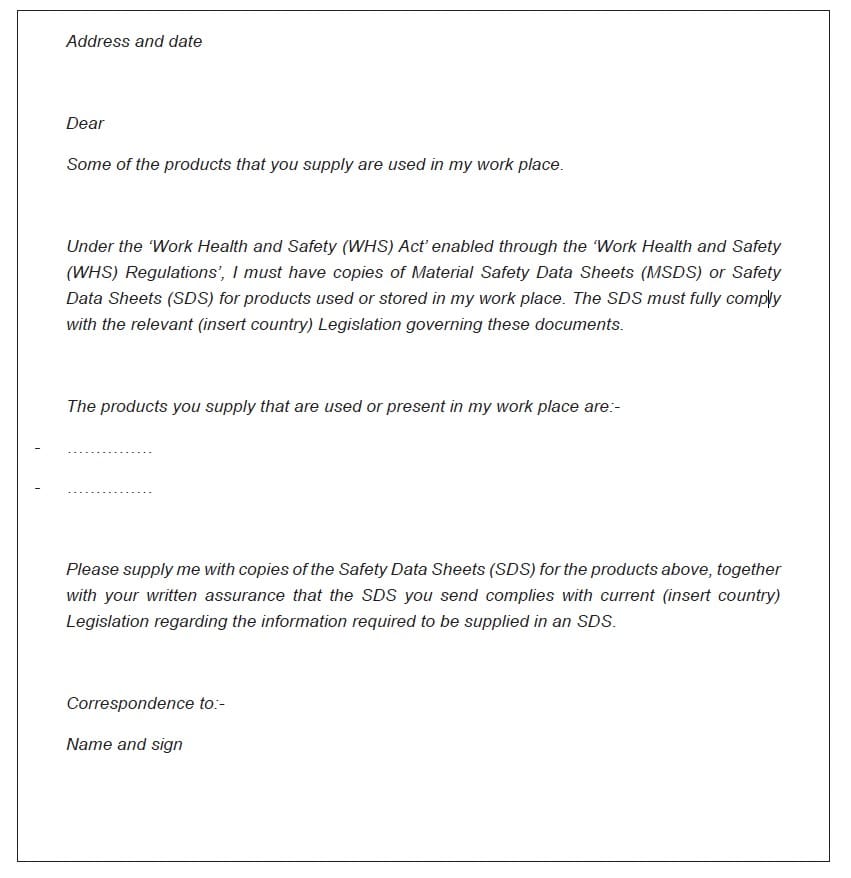
Whilst ‘Safe Working’ authorities can and do undertake inspections and audits, the reality, in this area of hazardous chemicals, is that compliance is largely enforced by exceptions brought to their attention via complaint, by reported harm or an accident occurring. It is at that point that any employer’s non-compliance will become apparent. It is important to realise that failure to comply with the relevant country WHS Act may result in significant fines and, if the non-compliance results in harm to workers, will result in criminal proceedings against the employer.
Understanding the MSDS or SDS
The objective of these documents is to enable workplaces to determine: – (i) if a substance (product) is hazardous or not, and if so then, (ii) What is the hazard and (iii) How to use the substance safely. The safety information in an MSDS or SDS is generally more detailed than that found on the product labels. Unfortunately the information in MSDS and SDS is often very detailed and uses “jargon” that can make it very hard for ordinary users to understand what it really means for them. This is partly because it also contains information only relevant to other people, for example:- The Transport Company; the Railways; the Fire Brigade; Medical Doctors etc. Also the information covers all the possibilities from one small container package through to a truck load, or warehouse full of the substance.
Mostly, the information relevant to flooring industry workers is easy to find in an MSDS or SDS’s when you know where to look. The headings/sections of the MSDS and SDS are practically identical and are listed below.
Headings/sections in an MSDS and SDS:-
MSDS | ||
SDS | ||
1. Identification of the Material and Supplier | 1. Identification: Product identifier and chemical identity. Details of the manufacturer or importer and emergency contact (including out of hours). | |
2. Hazards identification | 2. Hazard(s) identification | |
3. Composition/Information on ingredients | 3. Composition and information on ingredients | |
4. First Aid Measures | 4. First-aid measures | |
5. Fire Fighting Measures | 5. Fire-fighting measures | |
6. Accidental Release Measures | 6. Accidental release measures | |
7. Handling and Storage | 7. Handling and storage, including how the chemical may be safely used | |
8. Exposure Controls / Personal Protection | 8. Exposure controls and personal protection | |
9. Physical and Chemical Properties | 9. Physical and chemical properties | |
10. Stability and Reactivity | 10. Stability and reactivity | |
11. Toxicological Information | 11. Toxocological information | |
12. Ecological Information | 12. Ecological information | |
13. Disposal Considerations | 13. Disposal considerations | |
14. Transport Information | 14. Transport information | |
15. Regulatory Information | 15. Regulatory information | |
16. Other Information | 16. Any other relevant information |
The most important personal health and safety information is found at:-
2. Hazard(s) identification
8. Exposure Controls / Personal Protection
4. First Aid measures
Workplace safety can also require reference to:–
6. Accidental release measures (i.e. Spills small or large)
7. Handling and Storage
13. Disposal considerations
Hazard Identification
If the substance (product, or part of the product such as the hardener), is classified as hazardous or not
it will say so in the SDS (or MSDS) at Section 2.HAZARDS IDENTIFICATION (As per examples below).
In this section you will also see the ‘Risk Phrases’ (i.e. in what way is it hazardous) and the ‘Safety Phrases’
(i.e. how to handle the substance safely.
For example:-
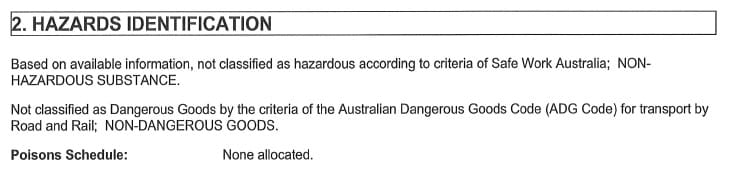
OR –
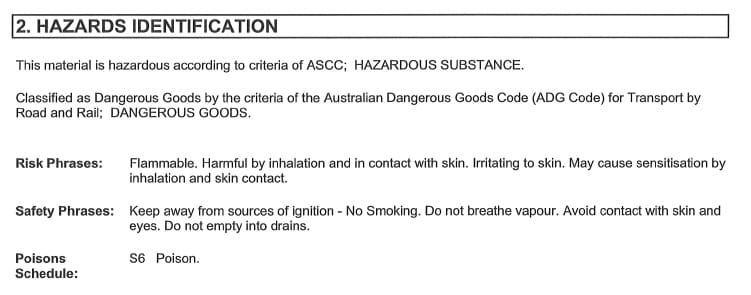
If you wanted to know more about exactly what is in the product that is causing it to be hazardous you would look in Section 3. Composition/Information on Ingredients.
GHS compliance requires one or multiple pictograms indicating the relevant hazard to be clearly visible on both the packaging of the product as well as on the SDS.
There are nine hazard pictograms in the GHS which represent the physical, health and environmental hazards. Some relevant examples include:
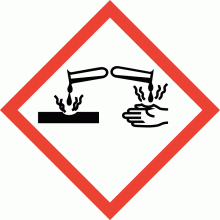
GHS05—Corrosion
Corrosive chemicals, may cause severe skin and eye damage and may be corrosive to metals
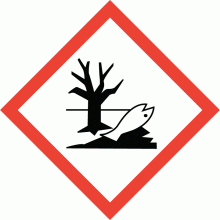
GHS09—Environment
Hazardous to aquatic life and the environment.
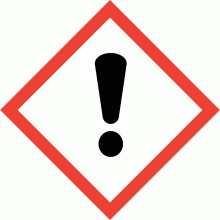
GHS07—Exclamation mark
Low level toxicity. This includes respiratory, skin, and eye irritation, skin sensitisers and chemicals harmful if swallowed, inhaled or in contact with skin.
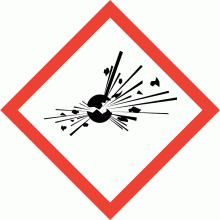
GHS01—Exploding bomb
Explosion, fire, blast or projection hazard.
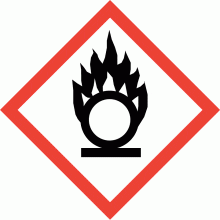
GHS03—Flame over circle
Oxidising liquids, solids and gases, may cause or intensify fire.
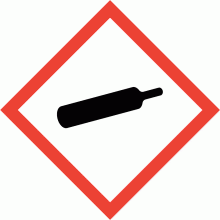
GHS04—Gas cylinder
Gases under pressure.
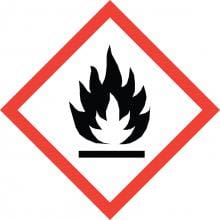
GHS02—Flame
Flammable liquids, vapour, solids and gases; including self-heating and self-igniting substances.
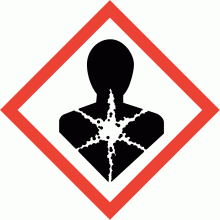
GHS08—Health Hazard
Chronic health hazards; this includes aspiratory and respiratory hazards, carcinogenicity, mutagenicity and reproductive toxicity.
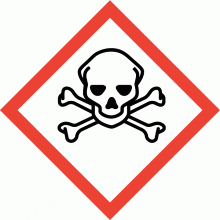
GHS06—Skull and crossbones
Fatal or toxic if swallowed, inhaled or in contact with skin.
What Next?
After you have checked the product label and the MSDS or SDS and determined if the product is hazardous or not, if it is hazardous in some way, what to do? Further reference to the MSDS or SDS is required. This is mainly to more fully understand the causes, effects and avoidance of risk in order to determine the action that may need to be taken.
For example:-
- What to do if a worker is accidentally or deliberately exposed to, or is overcome by the product?
Refer to Section 4. First Aid measures. - What if there is not sufficient ventilation in the working area?
Refer to Section 8. Exposure controls and personal protection. (For example below)
If inhalation risk exists due to processing vapours, wear organic vapour respirator meeting the requirements of AS/NZS 1715 and ASINZS 1716.
- What are the short term and long term effects of exposure to the product? Refer to Section 11. Toxicological Information
Our Responsibility
Remember, it is the responsibility of all of us to both understand and use hazardous products safely and not injure ourselves or others who may be around us when such products are being used.
It is also important to also realise that even water based products can be hazardous both to people and the environment and that Volatile Organic Compounds, VOCs, are not the only hazardous materials that can be present in the products used in our industry.
If there is any information in an MSDS or SDS that you do not understand but believe is relevant to you and/or your co-workers safety, you should request that the supplier arrange for a suitably qualified person to explain it to you or seek advice from your State or Country Government Occupational Health and Safety
authority.
For more information on ATFA’s recommended operator protocols when using coatings and adhesives please also refer to the policy statement – “ATFA Takes a Stance on VOC Ratings in Coatings and Adhesives”. (This can be found in the consumer information section of the ATFA website and in the grey ATFA Information Guide).