Owner expectations – Engineered, Laminate and Bamboo Floors - Consumers
This information sheet outlines reasonable owner expectations for engineered, laminate and bamboo floors. An acceptable finished floor will differ to that of solid timber flooring due to differences in product characteristics associated with manufacturing and installation processes.
Even within a flooring type, differences in both performance and appearance occur, as do manufacturer installation requirements. Specific installation techniques differ when products that are adhesive fixed to the subfloor are compared to those that are floated even when the same product is used. These product types are mainly manufactured in Europe and Asia and are therefore manufactured to differing overseas standards.
The ATFA has more detailed information on each product type and installation practices in their industry standards, available for purchase on the ATFA websites. A more general understanding can be gained from the brochure ‘Timber Flooring Applications’ also available on the ATFA websites.
Concerning floor acceptability, there are performance aspects affected by subfloor preparation and expansion requirements that require strict compliance to manufacturer installation instructions to maintain both the performance of the floor and warranties.
There are also aspects affecting performance that lie outside the installers control including moisture ingress, poor cleaning practices, improper use and climatic conditions that are outside of the manufacturer stated performance range for the product.
These aspects, as well as differences between the products types, need to be fully understood and appreciated by owners with it considered the responsibility of the flooring supplier/contractor to effective articulate product differences and any limitations to usage required by the manufacturer to ensure the warranty is maintained. Note that when the appearance of a floor is affected it is usually assessed from a standing position from an aspect that would be used during normal usage of the areas.
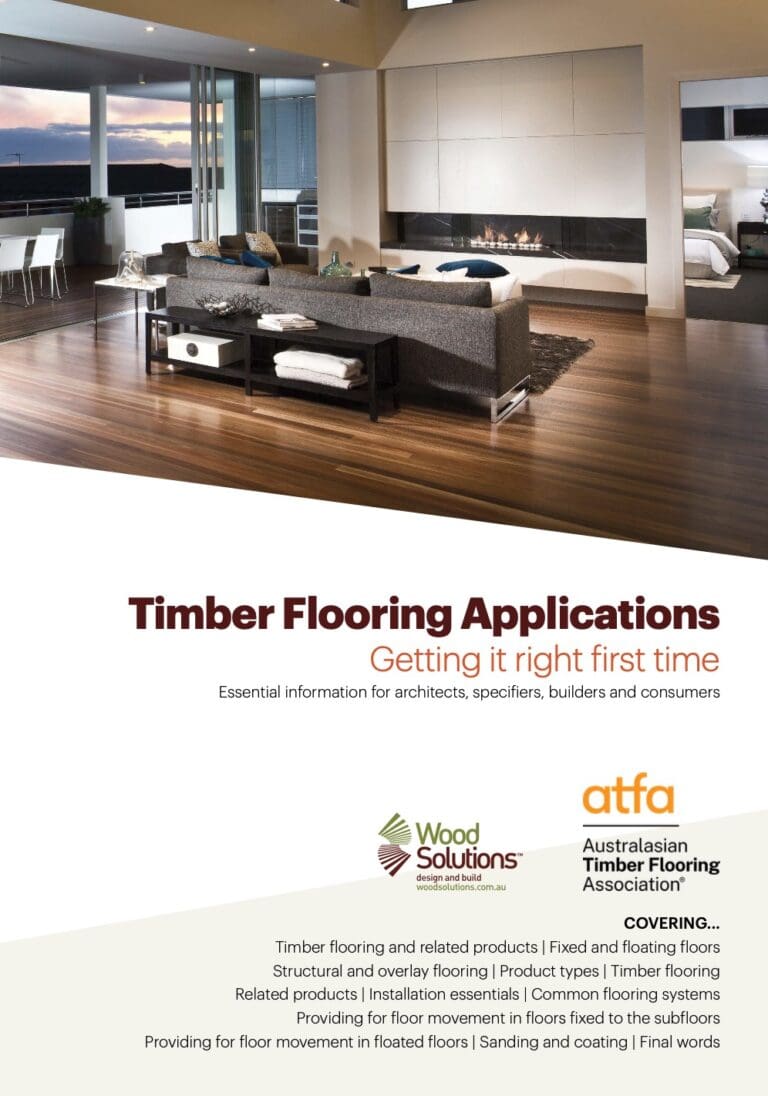
Acceptable floor performance
Floor flatness aspects
Both engineered and bamboo flooring may be adhesive fixed to the subfloor and as the fixing of each board is to the subfloor, these floors will act more like a solid timber floor. But each of these flooring types, engineered, bamboo and laminate are also installed as floating floors where boards are fixed to each other and not to the subfloor. With floated floors the total floor area often needs to be reduced into smaller areas or ‘rafts’ that are bridged with movement control joints. This is called compartmentalisation. However, irrespective of whether the floor is fixed or floated, in some circumstances the floor surface may not present as being flat. Below are some of the more common concerns relating to floor flatness or the flatness of individual boards. Generally, these should not occur in a floor although, and as outlined, if relatively minor can be considered acceptable.
Cupping – Cupping, with board edges higher than board centers, is generally associated with bamboo flooring and at times engineered flooring but not usually laminate flooring. The cause is often moisture from beneath the floor causing greater expansion of the lower board surface and this causes the cupped appearance.
However, with engineered flooring an imbalance in the moisture content of the face layer (lamella or veneer) can also cause boards to cup. Minor cupping can also be associated with a very dry internal environment. Consistent cupping that is visible throughout a floor in more than glancing light is not considered to provide an acceptable appearance and nor where the cupping is the result of moisture effects from beneath a floor.
However, where heating systems or direct sunlight impinge on a floor causing some localised cupping, it should be accepted. Maintaining conditions of low internal air relative humidity below the limit indicated by the flooring manufacturer would also be considered owner induced.
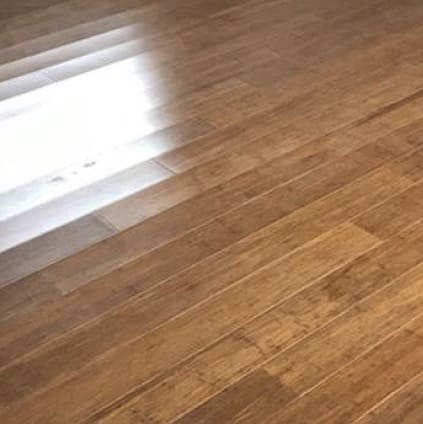
Excessive cupping in a floated bamboo floor from subfloor moisture beneath the floor
Crowning – Crowning, where the center of the board is higher than the edges, can be associated with engineered flooring but does not occur in bamboo or laminate flooring. When the floor is in an uncontrolled naturally ventilated environment, the flooring can be expected to absorb moisture from the humidity in the air.
This will often cause some swelling of the face lamella, but the overall effect on the board will differ depending on the board construction, face lamella thickness and also the ‘strength’ of the species in the face lamella. Crowning can also occur if the face lamella has been manufactured at a very low moisture content. It is therefore more common in flooring with high density thicker face lamellas and with floated as opposed to adhesive fixed floors.
Boards should not have a visibly crowned appearance when removed from new boxes and only minor crowning should be expected in an in-service floor.
As crowning is affected by air humidity, aspects of lamella species and thickness, installation method and manufactures stated optimum humidity range for the product, all need to be considered.
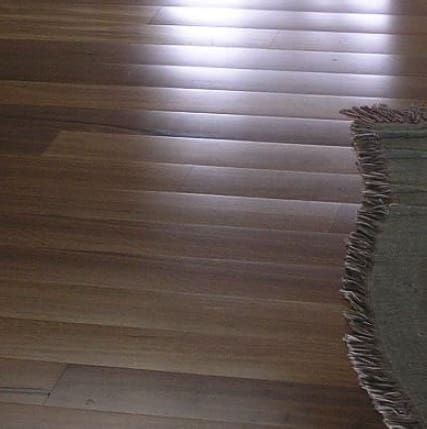
A floated floor crowning in the tropics with a high-density face timber. This degree of crowning is excessive.
Peaking and end-peaking – Peaking relates to raised boards edges but differs from cupping in that it is pressure related not moisture related. As well as raised board edges from pressure it is also possible to get raised board end-joints known as end-peaking. End-peaking can be from pressure effects and also from laying boards that are more severely bowed (boards with their ends more severely curved upward), causing end-joints to be proud. Peaking and end-peaking can occur in engineered, bamboo and laminate flooring and in floors that are floated and adhesive fixed.
But both forms of peaking can often be avoided if the floor in properly compartmentalised and with appropriate expansion allowance provided. Manufacturers generally indicate that in addition to perimeter movement allowance (accommodating shrinkage and swelling of rafts), floors across doorways can need control joints and a floor can only be of a certain width and length before intermediate movement joints are needed.
This is for both floated and adhesive fixed floors and noting that requirements are manufacturer, product and installation method specific. Insufficient expansion allowance and insufficient compartmentalisation can therefore be factors contributing to peaking and end-peaking. Product supplied at low moisture content or with pronounced bow can also contribute. Peaking or end peaking that is minor and only apparent toward glancing light sources may be considered acceptable.
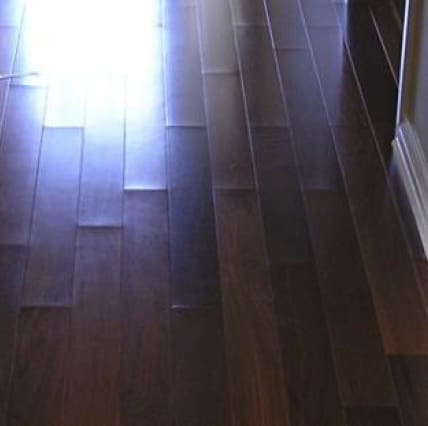
This is an adhesive fixed strand-woven bamboo floor with excessive end-peaking.
Telegraphing – This only occurs in block construction engineered flooring and has the appearance of regular stripes across the width of the boards. It can be due to both product manufacture and moisture effects causing differential swelling within the block core layer.
Manufactured related telegraphing can be caused by inconsistency in the thickness and moisture content of the blocks beneath the face lamella and products with thinner face lamellas will be more susceptible.
If a floor is moisture affected, then this too can cause differential swelling of the block core layer and cause telegraphing to develop in the moisture affected area.
If very minor and only apparent toward glancing light, it may be considered acceptable.
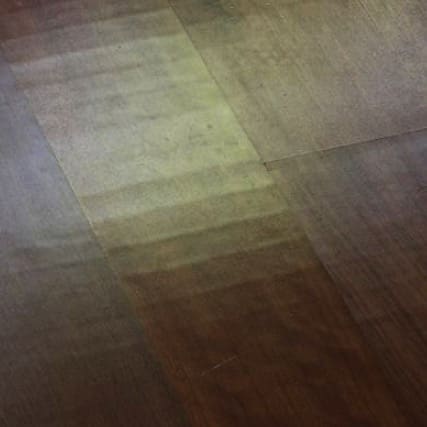
Telegraphing in an adhesive fixed engineered Oak floor.
Lamella and board delamination – In engineered flooring separation of the face lamella is considered a manufacturing fault that is covered by most warranties providing the fault develops in the floor after it has been laid. In such cases only the occasional board is usually affected and can usually be repaired.
Changes in the internal climate to a much drier in-service environment can create conditions that will stress the adhesive bond between layers and make boards more conducive to not only delamination of the lamellas but can also cause splitting of the plywood base layer in boards of that construction.
The splitting is often beneath the groove edge of boards having a tongue and groove (T&G) jointing system and this may correct itself with more humid conditions. Products can be expected to perform when the internal climate is within the specified acceptable humidity range indicated for the product.
Note also that localised hot dry conditions exceeding manufacturer acceptable ranges can be induced by more extreme use of heating systems.
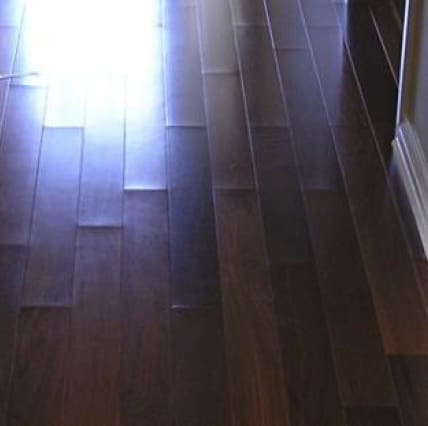
Lamella delamination
Buckling – This is mainly with floated floors and is where a section of boards rises up above the normal floor level.
A common cause is insufficient provision for floor expansion being incorporated into the floor at the time of installation. As indicated above, compartmentalisation is the breaking up of the total floor area into a number of smaller areas, often referred to as rafts, with the rafts connected by trims.
This along with adequate provision for expansion to all walls and vertical surfaces is needed to prevent buckling.
If a floor expands with insufficient allowance for movement being provided, then the floor will buckle and be in need of remedial work.
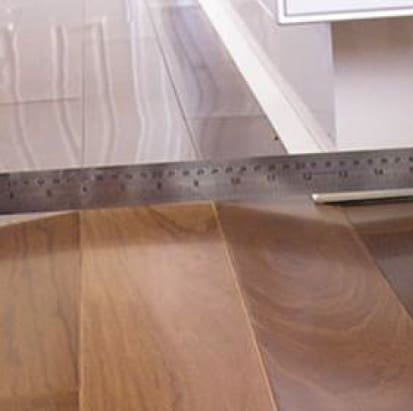
Buckling due to insufficient expansion allowance
Lipping – Lipping is the mismatch at board edges occurring between two boards within a floor. It can be felt mostly underfoot and particularly with square edge boards.
It generally indicates manufacturing imperfections but debris in joints on installation may also be a cause. In prefinished floors, some variation between board edge heights can occur with acceptable lipping less than 0.2mm for a square edge board and 0.5mm for a beveled edge board.
Some consideration also needs to be given to some additional variance occurring with flooring that has a textured surface.
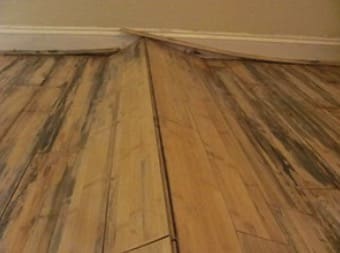
Swelled edges from moisture – Laminate flooring varies in its resistance to being affected by moisture and some laminate flooring is now manufactured as a water- resistant product.
However, no laminate flooring can sustain high levels of moisture over extended periods. With some products, spills need to be mopped up as soon as possible, others can sustain a spill for a few hours and moisture resistant products should not be affected by small spills.
If moisture is adsorbed at board edges or ends, the fiberboard core will swell and will remain in a swollen state even when the flooring dries. Product warranties generally outline the resilience of the flooring product to moisture ingress and should be viewed.
Board replacement is necessary to address boards that have swollen, provided spare boards are available.
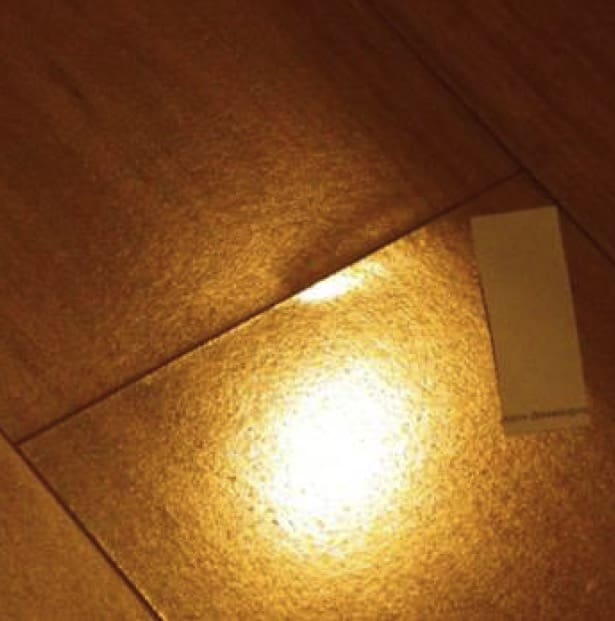
Moisture affected laminate flooring
Creaking and movement underfoot
To a degree timber floors are known to have an occasional creak or squeak, and this is often evident in older buildings. However, with products that are adhesive fixed, including solid timber flooring, squeaks or creaks with this installation method seldom occur. When it comes to floated floors laid on a foam underlay, no slab or other subfloor type is perfectly flat and it is therefore not unusual for floated floors to have some creak or other noise, as foot pressure will deflect board joints and rubbing within the joint can cause a creak sound when the floor is walked on.
Noise from a floor can be weather related and, in some instances, only occur when the floor is walked on for the first time each day. Factors that can contribute to noise from a floor are the flatness of the subfloor, slight buckling of the floor from insufficient movement allowance, underlay thickness, warp in the boards and board joint design with associated tolerances.
Each of these aspects affect the movement within board joints when the floor is walked on and highlights the importance of adhering to the installation instructions for the product and particularly subfloor flatness, underlay thickness and adequate movement allowance provided at installation.
Glueless jointing systems generally have waxed surfaces and this can assist with reducing noise but not necessarily prevent it. Noise that is not loud or only occurring in some areas of the floor is generally considered acceptable. However, if the noise is both very audible and present in main walkways or very audible and consistent when walking throughout most rooms in the house, remedial work needs to be considered.
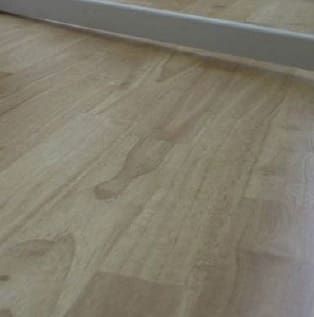
Buckling of the floor inducing creaking and excessive movement under foot
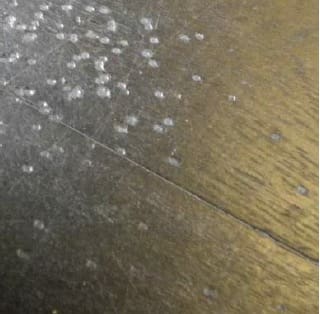
Oak is not a hard as Spotted Gum
Indentation and scratches
Indentations and scratches relate mainly to engineered flooring due to the variety of timber lamella species used and that these products are either factory coated, or site sanded and finished. Indentation resistance is governed by the hardness of the floorboard and this is influenced by the species, lamella thickness and core layer hardness.
When hardness is documented with engineered flooring, it usually refers to the published hardness of the lamella timber species and not the hardness of the engineered board. So, some care is needed when considering this. However, with much of the flooring having a lamella thickness of at least 2.5mm, a species of significantly lower hardness will be more prone to indentation than one with a higher hardness value. It is generally up to the purchaser to be aware of the hardness of the chosen flooring, with indentation seen as relating to floor care and not product manufacture or installation.
Scratching relates to the hardness of the coating, noting that the hard more brittle coatings often used on engineered flooring and bamboo are still susceptible to scratches. Again, it is considered that due care is needed by the owner to avoid scratching the floor as it is an owner responsibility. Engineered flooring coated with hardwax oil can be rejuvenated and be more easily repaired with this not generally possible with other coating types. If there was concern over the hardness of an applied coat, testing is possible. Laminate flooring has a surface layer of melamine which is very durable and under normal use will not scratch easily.
Hollow sounds
Flooring that is adhesive fixed to a subfloor and particularly concrete can have hollow sounds beneath boards. The primary concern with hollow sounds is a lack of adhesion, but it must be noted that floors will sound different depending on the evenness of the subfloor and depth of adhesive present.
As such, sound alone does not necessarily indicate poor adhesion. The occasional drummy board in a floor, with up to about 25% of the board area sounding hollow, is not considered a concern provided there is no vertical movement or significant vibration detected at board edges. In such instances there is no need to do anything about them.
However, in such instances if it is desired to deaden the sound in a more traffic-able area (e.g. a doorway) then it is accepted practice that a small hole can be drilled through the board and void filled. This practice can similarly be used for small areas of poor adhesion. If there is inadequate adhesion over a group of boards covering a wider area, then consideration needs to be given to replacing those boards.
Acceptable Floor Appearance
The overall appearance of engineered, laminate and bamboo floors can be affected by the surface appearance of individual boards and how the flooring has been laid. Some aspects such as board colour can also change with time as can the surface texture. Depending on the degree that the appearance is affected and whether it could be practically avoided will dictate acceptability.
Board length and laying pattern – When engineered, laminate and bamboo flooring is laid on a structural subfloor, products are often a set length for laminate or bamboo and either set length or nested lengths for engineered, with lengths commonly up to about 2.0m. Some products are however supplied longer length. At times engineered and laminate flooring is termed ‘one-strip’, ‘two-strip’ and ‘three-strip’ and this refers to the number of widths of face lamellas covering the base layer.
Hence two and three strip flooring have the appearance of ‘end matched joints’ aligning at the end of each board. The face of the board is also made up of many short to very short pieces and it is quite common with this type of product to have end joints in close alignment. With this product the general expectations for solid timber flooring do not apply where it would be usual to stagger end joints 300 to 450mm apart. But when the appearance is to replicate that of a solid timber floor, then general expectations are that the floor in terms of end joints will also be similar to those for solid timber floors. With floated floors some manufacturers also require end joints to be at least 150mm apart to ensure integrity of the locking system.
At times with set length boards there can also be an intention to create a regular pattern in the floor. Therefore, there are few specific requirements when it comes to laying patterns with these products and it requires discussion between the parties prior to floor installation. Do not assume the other party has a similar view on board layout to you. Also, the only requirements are those if specified in installation instructions.
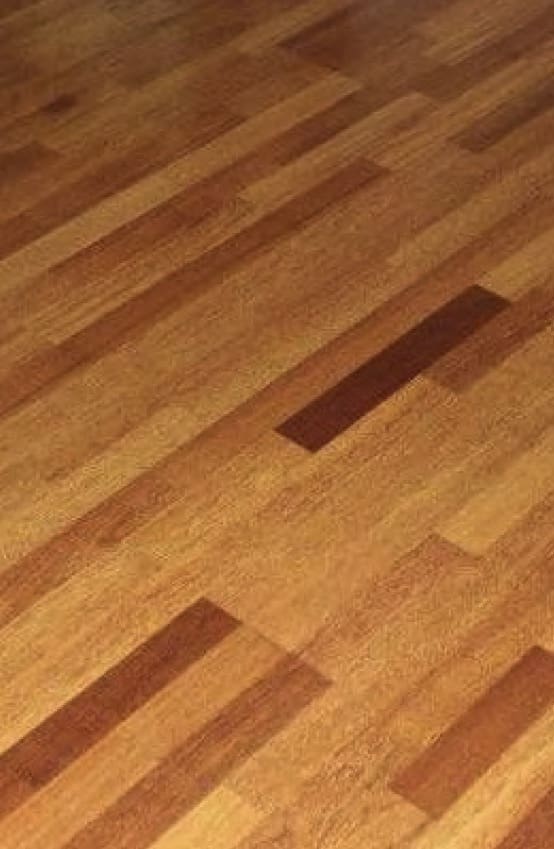
A 3-strip engineered floor
Surface checking – A check is a separation of the wood fibers and shows as a split in the lamella surface of engineered flooring. Such checks can be present at the time of manufacture and are filled, along with other open features. These are considered as a characteristic of the product.
However, post manufacture checking can occur in boards both prior to and after laying. Checking is also influenced by the internal conditions. Very high humidity that can cause crowning, will also stress the face lamella and may result in checks. Similarly, a very dry internal environment or intense unfiltered direct sunlight can result in boards checking. Hence, owners also have a responsibility in looking after their floors. If the checks are more extensive across the floor and not associated with very dry internal conditions, then manufacturing aspects may need to be considered.
Minor checking after installation in a limited number of boards is not usually a reason for concern and if checking is observed prior to laying that section of the board should be removed.
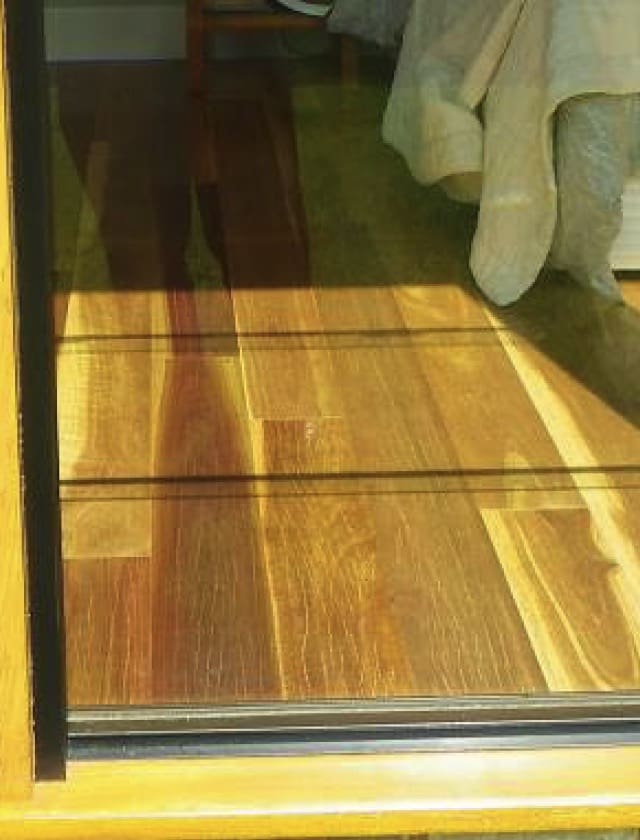
Intense unfiltered sunlight causing checking is an owner responsibility
Gapping at edges and ends – Many engineered, laminate and bamboo flooring products have glueless jointing systems for both edge and end joints and with such systems no significant gapping at board edges and ends should be expected. Some engineered and bamboo flooring has a tongue and groove (T&G) jointing system and if laid as an adhesive fixed floor they will be more like a solid timber floor and minor gapping can occur. If boards with a T&G jointing system are floated, then adhesive used in the T&G joint, that should prevent any significant gapping at board edges and ends.
Minor gapping is possible in installations of all types due to seasonal movement and boards not being absolutely straight down their length, and such minor gaps are generally not highly noticeable and are to be accepted. In some cases, a filler may be used if of concern.
Wide gaps and particularly where the jointing system has separated, requires remedial work. Note that with floated floors, if insufficient attention is given to subfloor flatness, compartmentalisation and underlay thickness, then board separation can occur.
Similarly, the design of the locking system and particularly at end joints can play a role. Insufficient or inadequate adhesion and if crosslinked PVA is not used in T&G joints, this can also lead to board separation in that type of flooring.
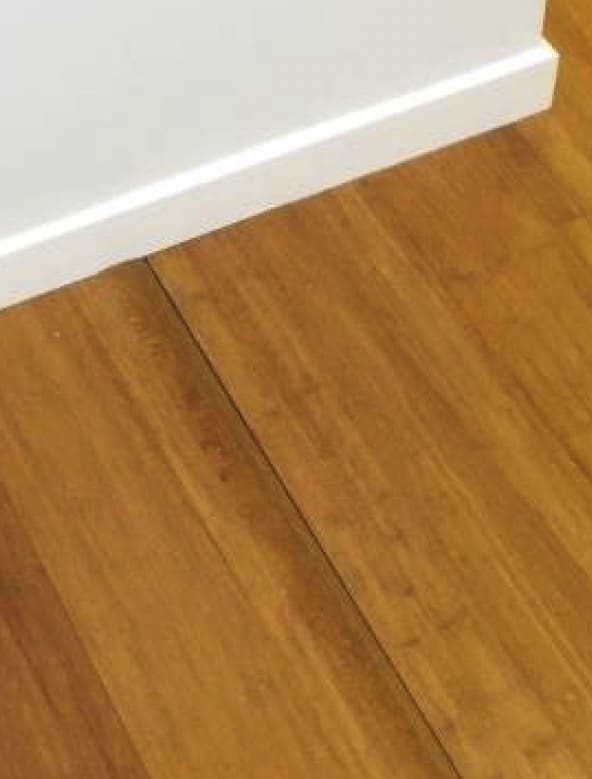
Board separation due to insufficient compartmentalisation
Colour – At times flooring is selected based on species and at other times, particularly with pre-finished flooring on both coated colour and texture of the boards. Some coloration disguising the species while other coatings enhance the species appearance.
Concerns with colour are usually associated with engineered flooring as laminate flooring usually has a set number of images and thereby consistency across batches and bamboo flooring a more uniform appearance.
It needs to be considered that particularly with engineered flooring there will be changes in timber and coating colour over time and if the flooring is partly covered by floor mats, a difference in colour tone will occur. In some instances, the variation in tone will be more subtle but in other instances more intense.
On a new floor the laying of floor rugs should be delayed which allows the whole floor to change colour more evenly, noting that colour change reduces with time. In most instances colour change needs to be accepted as a natural characteristic of the product
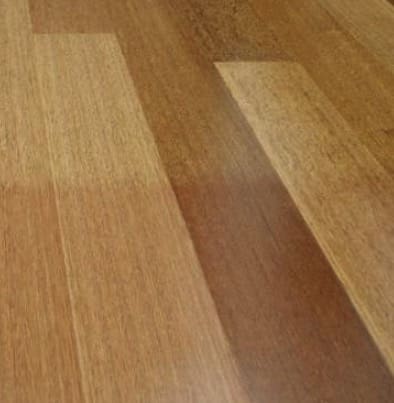
The floor presents as being darker where it had been covered by a rug
Grade – Grade relates to the features (such as knots or gum veins) in a board and such features add character to a floor. Often engineered flooring is sold based on the appearance of samples and brochures with no particular grade being specified.
Some flooring with Australian species in the face lamella may however be graded to the rules of its solid timber counterpart. With Oak flooring the grade is often specified as ABCD grade, but the rules around this can vary depending on the country of origin. This grade name is really a mix of grades, with some boards having a lot of feature and other boards minimal feature.
Concerns arise when the flooring has a different appearance in terms of features to what the purchaser was expecting. This is usually more feature in the boards rather than less but also may relate to the size of features or the filling of open features. Aspects relating to grade can therefore be quite vague and it is important that parties have a clear understanding on aspects relating to the amount of feature, the size and the filling of open features at the time when product is selected.
Small samples or photos do not often convey a realistic perspective of what can be expected. And again, do not assume the other party has a similar view to you. Purchasers also need to realise that every floor is unique and will differ from others in the same product that they may have viewed
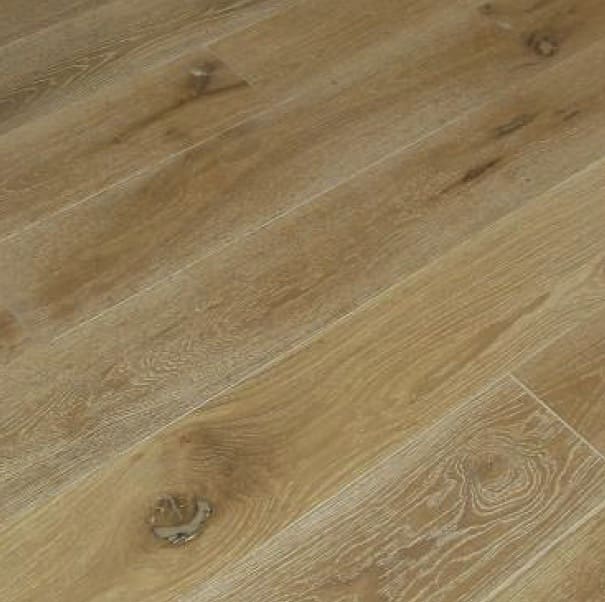
An ABCD grade Oak floor coloured to enhance the grain and with open features filled
Finishing and trims
All these flooring products will swell and shrink with changing weather and internal conditions and installation methods have been developed to accommodate this movement. Particularly with floating floors, trims are an essential part of the installation. As indicated above, several of the problems with floated floors are due to insufficient movement allowance being provided in the floor.
Providing appropriate movement allowance for the product, in its laying environment, is a must not an option. When trims, scotia and skirting are installed, it should be expected that that they are securely fixed but not to the flooring, and that they provide for unrestricted movement of the floor. It is for this reason and particularly with floated floors that the caulking of gaps to vertical surfaces and to the likes of skirting should not occur.
Restriction to natural movement of floor will generally be considered an installation problem. When trims and scotia are installed it is expected that they would provide a neat and tidy finish and complement the floor installation in terms of appearance.
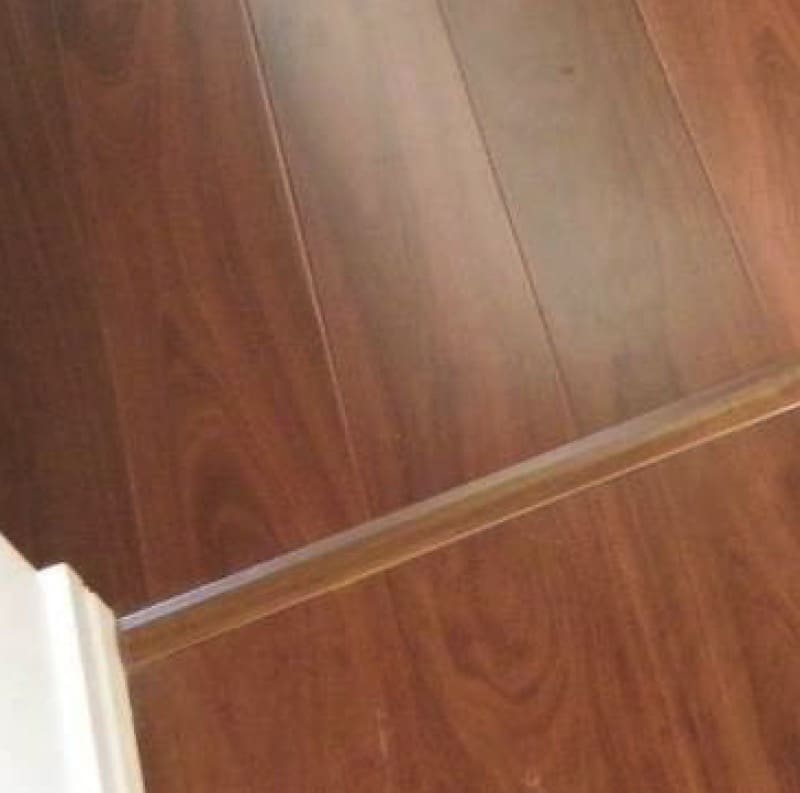
Control joint across a doorway
Summary
In line with the ATFA industry standards relating to these products, manufacturer’s installation instructions must be understood and followed and in doing so this will negate many of the issues related to the performance and appearance concerns with these floors.
Performance aspects such as minor checking, cupping and peaking are also not necessarily manufacturer or installation related and the owner also has a responsibility in the care and maintenance of the floor with it expected that clear concise maintenance instructions will be provided to the owner by the retailer or contractor.
Due to product and installation tolerances, there will be some minor imperfections affecting the performance and appearance of the floor that need to be accepted, but also noting that in other instances greater remedial work is required to bring a floor to a commercially acceptable standard.
Floor preparation and provision for movement (shrinkage and swelling) are two aspects that when not adequately accommodated for, can result in a variety of problems including boards creaking. In terms of appearance aspects, it is necessary that owners have a clear understanding on what the product is that they are purchasing (e.g. grade), and the characteristics inherent of the installation method used. The owner and those involved in the installation also need to discuss aspects where there is a choice such as laying pattern or species hardness. As such each party should have similar expectations and can be pleased with the outcome