OWNER EXPECTATIONS – SOLID TIMBER FLOORS
This information sheet outlines reasonable owner expectations for onsite sanded and coated timber floors, which generally applies to solid T&G flooring and parquetry. Concerning floor acceptability, there are performance aspects of the floor which can relate to fixing integrity, board shape and movement, and then there are appearance aspects which focus more on the sanding and finishing.
The sanded and coated appearance aspects of this information sheet will also be applicable to some other flooring types (e.g. engineered flooring that receive site sanding and coating). Although an imperfection free floor is the desire of any tradesperson, it is the process of installation and finishing where the environment and other conditions cannot be fully controlled that moves the completed job to one that is ‘normal’ and of a commercially accepted standard. This however is not to say that the completed floor won’t be of a high standard and well suited to its purpose as a floor, which is to be walked on, but it does acknowledge that the finished product will not be the same as fine furniture and that due to seasonal influences and heating and cooling, that some movement reflecting the nature of timber will occur.
Concerning the installation of the floor, the provisions are outlined in either the ATFA publication ‘Solid Timber Flooring – Industry Standard’ (2016) or specific manufacturer recommendations for their products. The sanding and finishing of timber floors is covered by AS 4786.2 – Timber Flooring – Sanding and Finishing along with more current practices provided in ‘Solid Timber Flooring – Industry Standard’ and other ATFA information sheets.
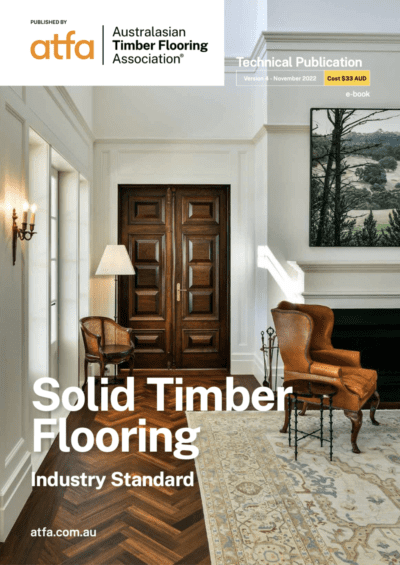
Acceptable floor performance
Even board surface
The following section outlines some problems that affect the surface of the boards and these should not generally occur in timber floors.
However, floors exposed to heat sources after occupancy (e.g. no curtains, fireplaces, vents from appliances, houses closed up for extended periods) can cause movement in the flooring resulting in effects such as greater gapping or cupping in the affected area. Similarly, changes that affect the conditions beneath a floor can also result in board movement and shape changes such as cupping and peaking. It should be noted that the actions or inaction of owners and builders can contribute, or even cause these effects to occur.
Therefore it is beneficial for flooring contractors to make builders and owners aware of aspects that could affect their floor and that any concerns that the builder or owner has, be brought to the attention of the flooring contractor at an early stage. Product choice, particularly in terms of board width, and also the installation method will influence in-service movement and noting that wider or thin boards can be more prone to some cupping and gapping in a dry internal environment. The conditions outlined below should however not normally occur in a floor and if they do, remedial work is often necessary.
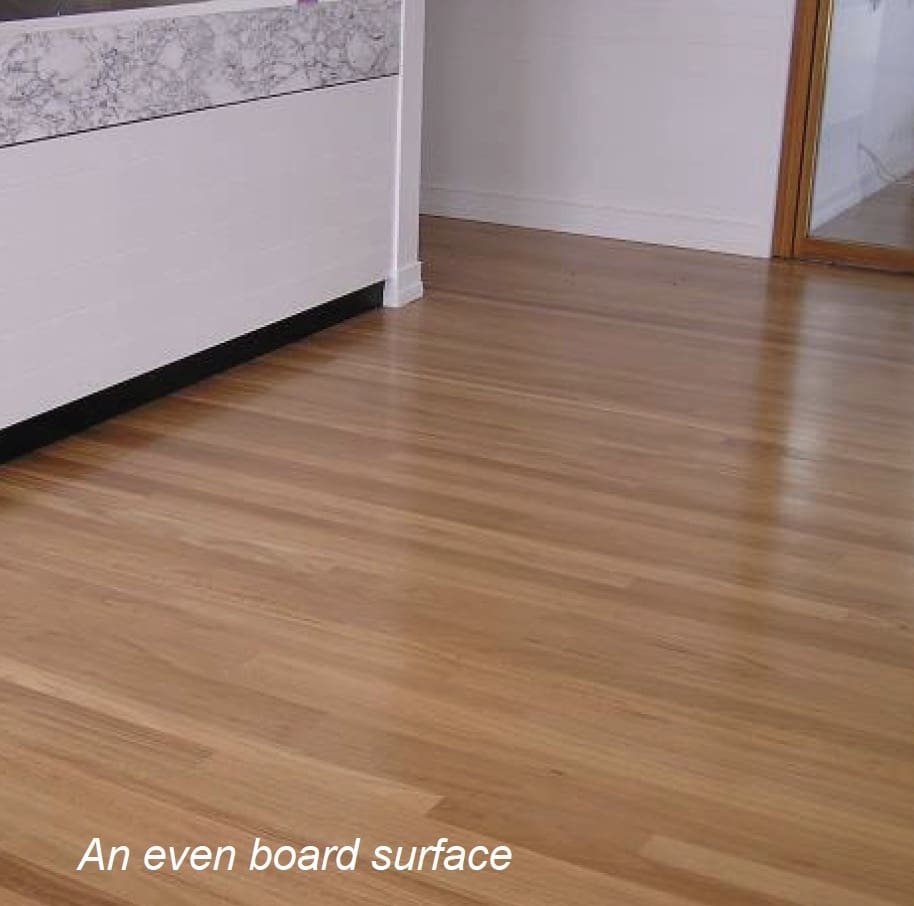
- Cupping – boards with their edges either higher or lower than the centre of the board. Heat in a specific location or a very dry environment above the floor may result in cupping. Moist subfloor spaces can also cause boards to cup. Cupping is more likely to be observed in overlay flooring and standard thickness boards that are wider than 100 mm. To some degree a small amount of observable cupping may occur in some locations within a dwelling (e.g. sun exposed floor) where these types of flooring are used.
- Peaking – this has the appearance of cupping but is the result of expansion pressure in the floor.
- Tenting – two adjacent boards, where the adjoining edge has lifted above the level of the adjacent flooring. This is often associated with high moisture beneath the floor and can be from many causes.
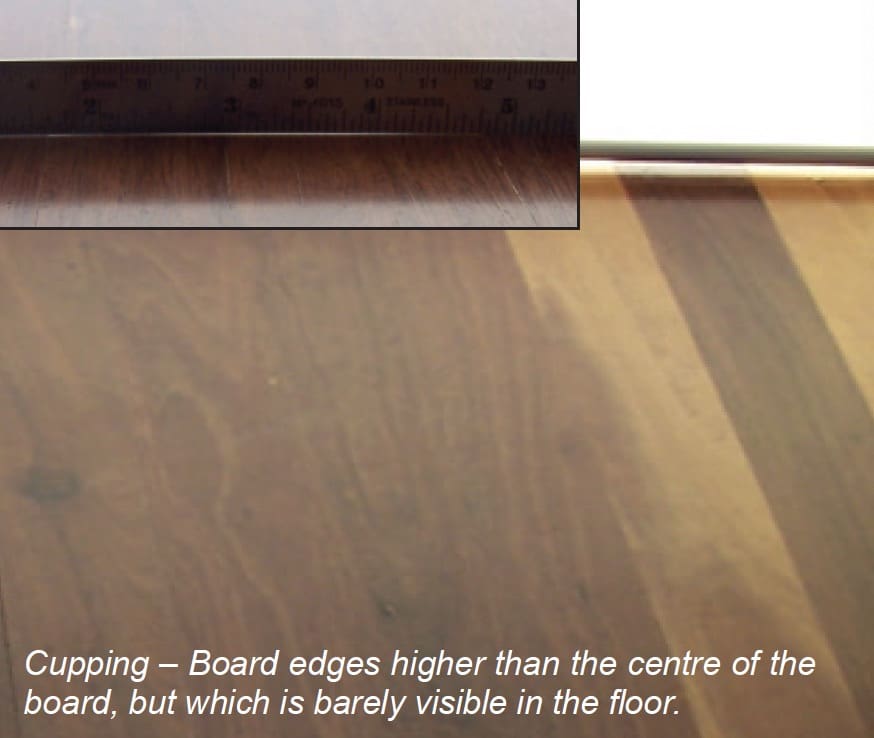
- Buckling – a section of flooring containing a number of boards that is raised above an adjacent section.
- Crowning – floorboards that are flat on their lower surfaces but where the upper surface has its edges lower than the centre of the board. Crowning in timber floors occurs when a floor has become wet, has cupped and then is sanded prematurely before the moisture imbalance between the top and bottom of the board has balanced out. Crowning does not become apparent until some months after finishing.
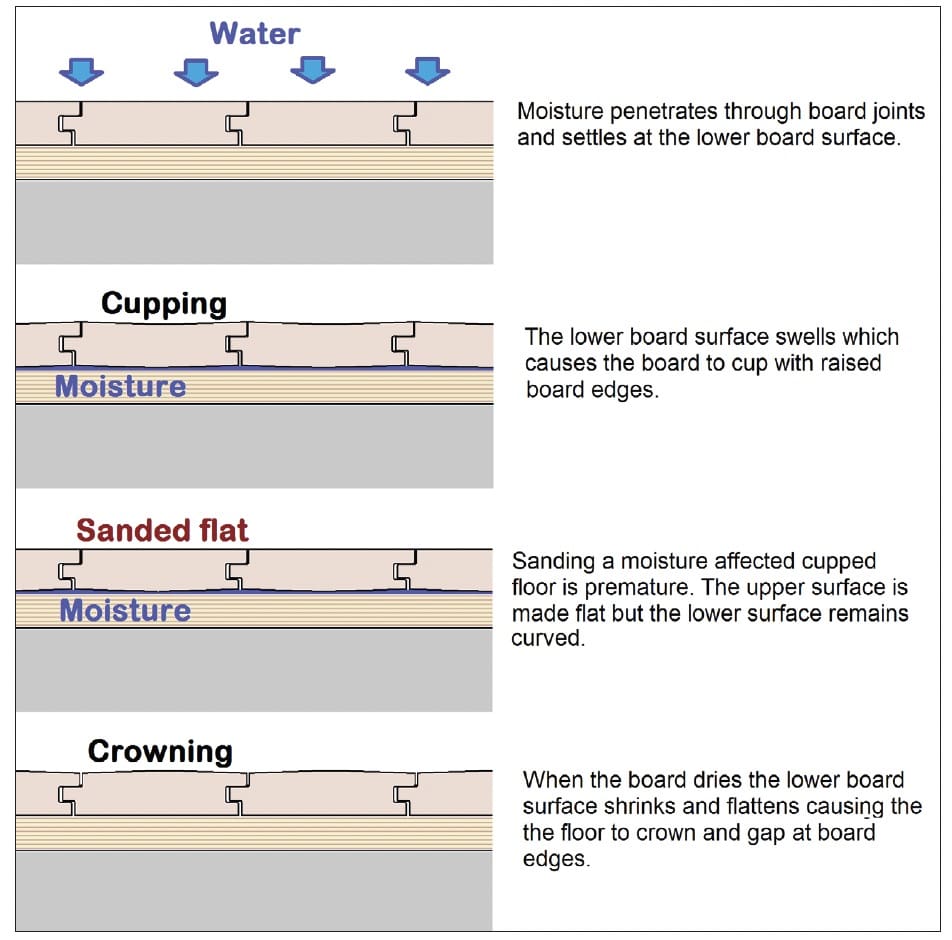
Limited vertical movement at T&G joints
Flooring is manufactured with the board tongue narrower than the groove. This is necessary so that boards will fit together during installation. When floorboards are laid over joists or battens, some differential vertical movement may occur between adjacent boards, when a load is applied to an individual board. This is due to the clearance between the tongue and the groove. The clearance should not exceed 0.6 mm.
Relatively even gapping between boards in areas not exposed to specific heat sources
With solid timber strip flooring shrinkage gaps over 10 boards can average 0.75 mm for an 80 mm wide board floor under drier internal conditions. For wider boards, proportionally wider average gapping can be expected. The appearance should indicate gapping between most boards and be free from irregularly spaced wide gaps associated with edge-bonding. The provision of expansion gaps as part of the installation process and evident throughout the life of the floor is acceptable.
The first photo which is considered acceptable, has gapping near the upper limit where the average gap size was 0.75 mm and the second photo has gapping that is not considered acceptable where the average gap size was 1.8 mm. Note that it is the average gap size over 10 boards so some gaps are greater than the average and other less than the average.
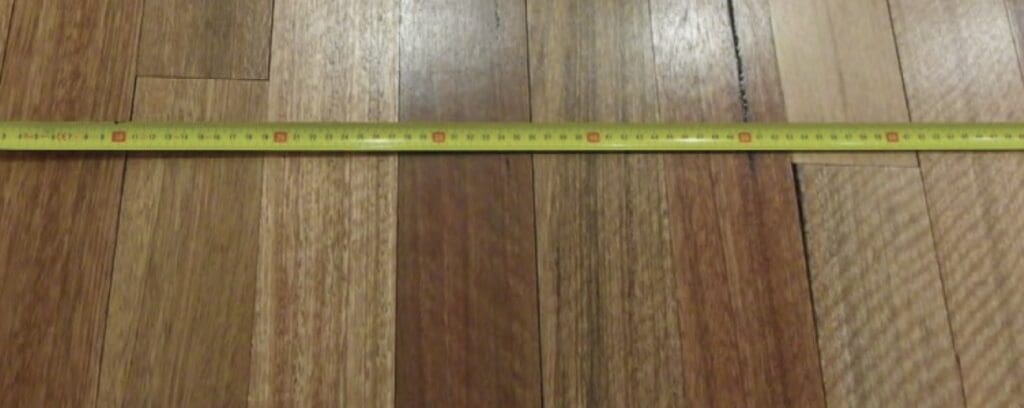
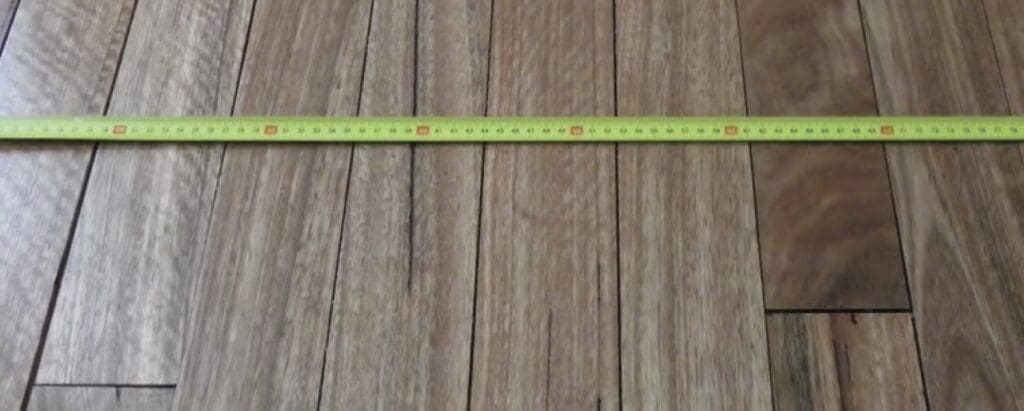
Minimal squeaking
A small amount of noise can be expected from most timber floors, when walked on. Noises can occur from movement of one board edge against another or from boards moving on nails. A floor is often more noisy during drier weather due to loosening at the joints. If squeaking is present in main trafficable areas then remedial repairs should be considered.
Indentations
Timber strip floors can be expected to show some indentations depending on the hardness of the species used, volume of traffic, active pets and footwear worn. Softer timber will indent more readily than harder timbers.
Hollow sounding spots
When timber floors are laid direct to concrete slabs, hollow sounding or drummy sounds can occur under some boards. When there are a limited number of instances associated with one or two boards in some areas of the floor, and no vertical movement when pressure is applied, remedial work is unlikely to be required.
Acceptable Floor Appearance
Acceptability considerations
There are no standards that outline what an acceptable appearance of a timber floor should be, although AS 4786 – Timber Flooring – Sanding and Finishing provides guidance in an appendix. When recommended sanding and finishing practices are undertaken, there is a general level of acceptance of the finished product in the marketplace. That is a commercially acceptable floor. Floors of the same species can differ markedly in their appearance depending on timber source, age of the tree, board cover width, the finish system used and the lighting in which the floor is viewed. Timber is
Acceptable Floor Appearance
Acceptability considerations
There are no standards that outline what an acceptable appearance of a timber floor should be, although AS 4786 – Timber Flooring – Sanding and Finishing provides guidance in an appendix.
When recommended sanding and finishing practices are undertaken, there is a general level of acceptance of the finished product in the marketplace. That is a commercially acceptable floor. Floors of the same species can differ markedly in their appearance depending on timber source, age of the tree, board cover width, the finish system used and the lighting in which the floor is viewed. Timber is
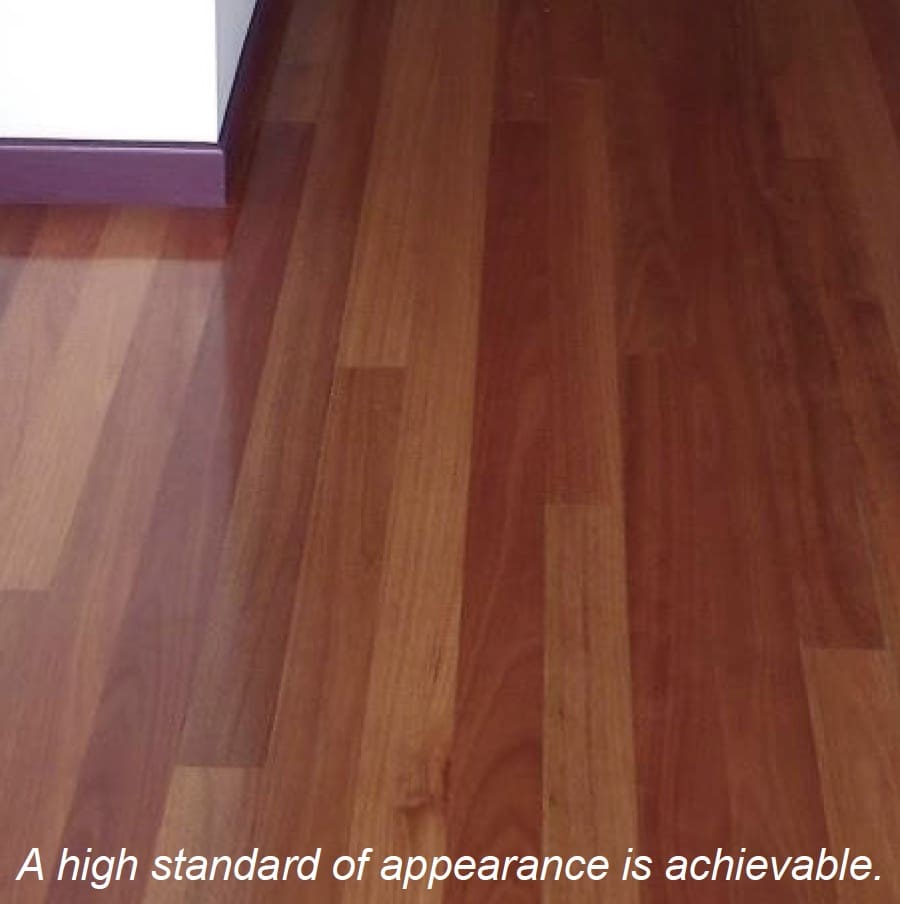
Timber is a natural product that will shrink and swell in response to changes in atmospheric humidity, no one building environment is the same as another and these aspects can also lead to differences in appearance. The sanding and finishing is not undertaken in a factory environment and the appearance of the floor may either darken or lighten with time, depending on the timber species and coating used. The home environment is also not dust free. However, the finished floor can be expected to have an even appearance free from heavy sanding marks and severe or frequent coating imperfections. A minimal level of contaminants, minor sanding marks and small depressions of the finish at board edges and in nail holes etc. may be visible and the perimeter and other hard to get at places are more likely to contain these irregularities. Due to this, a mirror finish or imperfection free floor is an unachievable expectation.
When floors are inspected for imperfections, the floor is to be inspected during daylight hours with lighting on. The overall assessment of the floor is from a standing position with the floor viewed from positions that are usually occupied by people. Internal and external reflections in areas not usually covered by furniture should be assessed. Acceptability relies on judgment that takes into consideration the effect of lighting on noticeable surface imperfections, as well as initial wear of the floor, which can cause some imperfections to significantly lessen or disappear. A floor is subject to much heavier wear than furniture and although a good quality finish can be expected, the same finish quality to furniture should not be expected.
Colour, species and grade
The overall colour or blend of colour in a floor is dependent on the species or species mix chosen. The character present in a floor, such as gum veins, are determined by those features permitted by the grade. Even when a single species is chosen there can be a wide variation in colour and it is also possible that a limited number of boards of a different species may be present due to similarity in appearance. It is also important to realise that grading rules do not cover either colour or colour variation. Grade names (e.g. Select) that do not align with the Australian or New Zealand Standards (e.g. Prime) are likely to be similar to those in these standards but clarification should be sought regarding differences.
The grading process is rapid and relies on quick visual assessment where graders must assess the size and extent of a feature without relying on measurement. Due to this some inaccuracy in grading can occur that may result in a limited number of boards that are outside grade limits.
The sanding of a floor can also increase the size of some features or cause features to appear that were not present prior to sanding. Consequently, some boards in a finished floor may not meet the specified grade description. The presence and development of such features needs to be acknowledged and accepted by those purchasing timber floors. When viewing a floor there is generally a clear difference between a floor that is of the incorrect grade and a floor where grade limits have been exceeded in some boards.
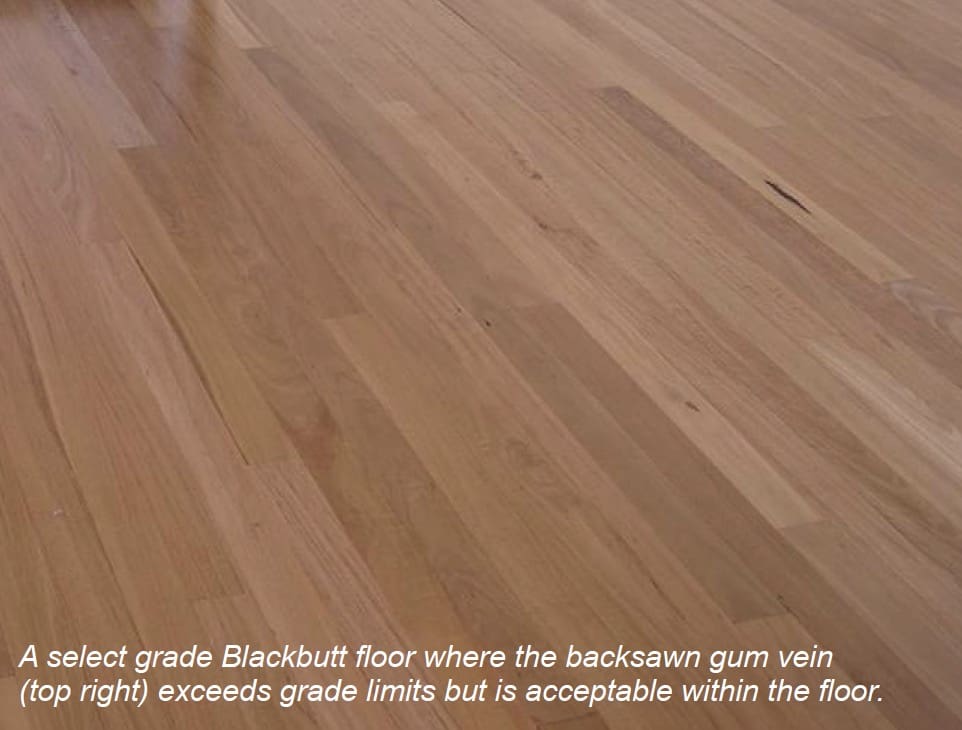
Where the number of boards in a floor that has features that exceed grade limits, in terms of size and number, are relatively few (less than 5%) and the overall appearance of the floor is in line with the chosen grade, no remedial work is considered necessary.
Grading also does not account for the distribution of features, in boards, between boards within a pack of flooring or within a finished floor. As such it is a reasonable expectation that the installer, when laying the floor, will provide a relatively even distribution of colour and feature throughout the floor. With regard to colour, however, it must also be recognised that coating a floor highlights colour differences and the extent of the change is at times not easy to discern. Similarly it can be expected that board lengths will be relatively evenly distributed in the floor and that groups of short boards or board ends will not be frequently clustered together.
Board lengths and distribution in the floor
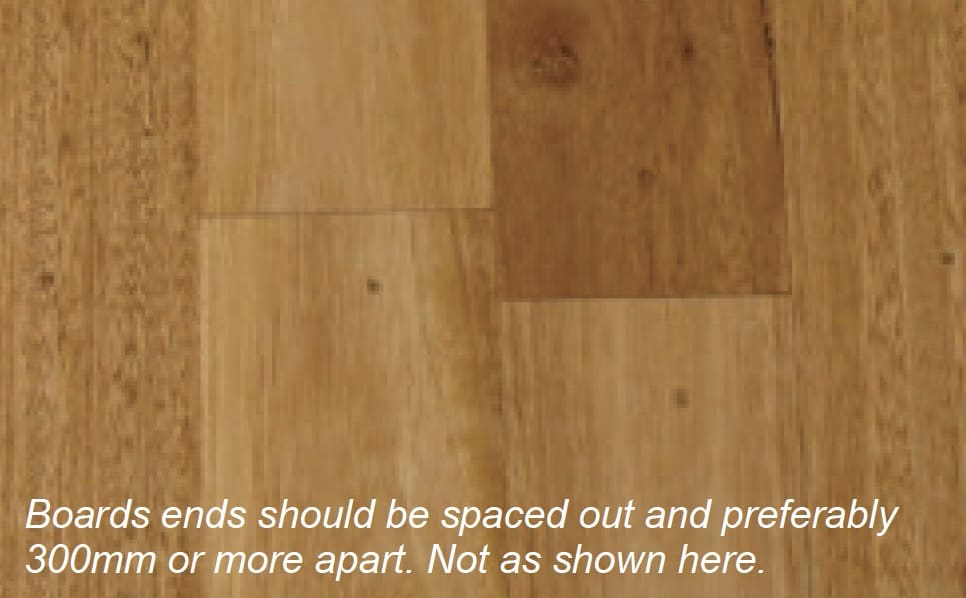
Board lengths for structural flooring (minimum 19mm thick) are generally a minimum of 900 mm long when laid on joists or battens. In structural floors boards should also span two joists or battens and only one end join should occur in a group of three adjacent boards between floor joists or battens.
When laying over a structural sub-floor the minimum length may be shorter. Where possible end joints should not cluster together or align. It is preferred that end joints be a minimum of 300mm from end joints in adjacent boards.
Sanding
The sanding process involves hand controlled equipment and due to this there will be some evidence of the sanding process in the floor. It can be expected that the floor will be fine sanded and that edging will not result in scalloping. Similarly it can be expected that corners will be scraped to an even surface and sanded to provide a fine surface. As such, sanding marks in the timber should not generally be visible from a standing position. The viewing angle for assessment should be 45° from the eye to the floor. At times there can be vibration that occurs which may be induced by the sanding machine or the subfloor framing. Although this vibration can lead to chatter marks in the floor, it would be usual to expect a floor free of chatter marks. With the re-sanding of an older floor it must also be recognised that the sanding process will not remove existing deep cuts or damage and that stains may also not be removed if they have penetrated deep into the timber.Nail Holes and Filling
Unless otherwise requested, all flooring nails are to be punched below the surface and the nail holes are to be filled. With solid T&G flooring it can also be expected that any gaps at board ends will also be filled. Filling at board edges is generally not recommended on new floors except for parquetry where flood filling is to be undertaken and in some instances with direct adhesive fixed floors. When one colour of filler is used, that colour should match the darker tone in the boards as with time the contrast generally becomes less with oil and solvent based finished. This is not necessarily the case with water based coatings.Coating and Finishing
A floor is subject to much heavier wear than furniture and although a good quality finish can be expected, the same finish quality to furniture should not be expected. There are a number of imperfections that are likely to be present to some degree in a finished floor and the degree to which they occur, where they occur and the presence of other imperfections, will determine their acceptability. When assessing the appearance of a floor it is to be done from a standing position and the floor should be viewed at an angle of about 45°. Common imperfections present to some degree in floors are outlined below.- Dust and debris – A degree of contamination in the final coat is unavoidable and will vary from one site to another being dependent on a number of factors such as draughts, heating and ventilation systems, insects and the like. It can be expected that the contractor will take reasonable measures to minimise the risk of contamination and that at job completion there will not be heavily contaminated areas in the floor that are obvious when assessing the floor.
- Swirl marks – Swirl marks are caused by rotary sanders and to some degree will be present in all floors. Down lights will highlight sanding imperfections due to light refraction through the coating and as such this is not controllable by the contractor. Fine swirl marks that are not obvious under natural light when assessing a floor should not be a concern.
- Coat levelling – Rejection, orange peel and quilting all relate to unevenness in the coating resulting in either a mottled effect or in the case of quilting discontinuity across joints. If instances are isolated, minimal in nature and not in areas frequently viewed then remedial work is unlikely to be necessary.
Sanding
The sanding process involves hand controlled equipment and due to this there will be some evidence of the sanding process in the floor. It can be expected that the floor will be fine sanded and that edging will not result in scalloping. Similarly it can be expected that corners will be scraped to an even surface and sanded to provide a fine surface. As such, sanding marks in the timber should not generally be visible from a standing position. The viewing angle for assessment should be 45° from the eye to the floor. At times there can be vibration that occurs which may be induced by the sanding machine or the subfloor framing. Although this vibration can lead to chatter marks in the floor, it would be usual to expect a floor free of chatter marks. With the re-sanding of an older floor it must also be recognised that the sanding process will not remove existing deep cuts or damage and that stains may also not be removed if they have penetrated deep into the timber.
Nail Holes and Filling
Unless otherwise requested, all flooring nails are to be punched below the surface and the nail holes are to be filled. With solid T&G flooring it can also be expected that any gaps at board ends will also be filled. Filling at board edges is generally not recommended on new floors except for parquetry where flood filling is to be undertaken and in some instances with direct adhesive fixed floors. When one colour of filler is used, that colour should match the darker tone in the boards as with time the contrast generally becomes less with oil and solvent based finished. This is not necessarily the case with water based coatings.
Coating and Finishing
A floor is subject to much heavier wear than furniture and although a good quality finish can be expected, the same finish quality to furniture should not be expected. There are a number of imperfections that are likely to be present to some degree in a finished floor and the degree to which they occur, where they occur and the presence of other imperfections, will determine their acceptability. When assessing the appearance of a floor it is to be done from a standing position and the floor should be viewed at an angle of about 45°. Common imperfections present to some degree in floors are outlined below.
- Dust and debris – A degree of contamination in the final coat is unavoidable and will vary from one site to another being dependent on a number of factors such as draughts, heating and ventilation systems, insects and the like. It can be expected that the contractor will take reasonable measures to minimise the risk of contamination and that at job completion there will not be heavily contaminated areas in the floor that are obvious when assessing the floor.
- Swirl marks – Swirl marks are caused by rotary sanders and to some degree will be present in all floors. Down lights will highlight sanding imperfections due to light refraction through the coating and as such this is not controllable by the contractor. Fine swirl marks that are not obvious under natural light when assessing a floor should not be a concern.
- Coat levelling – Rejection, orange peel and quilting all relate to unevenness in the coating resulting in either a mottled effect or in the case of quilting discontinuity across joints. If instances are isolated, minimal in nature and not in areas frequently viewed then remedial work is unlikely to be necessary.

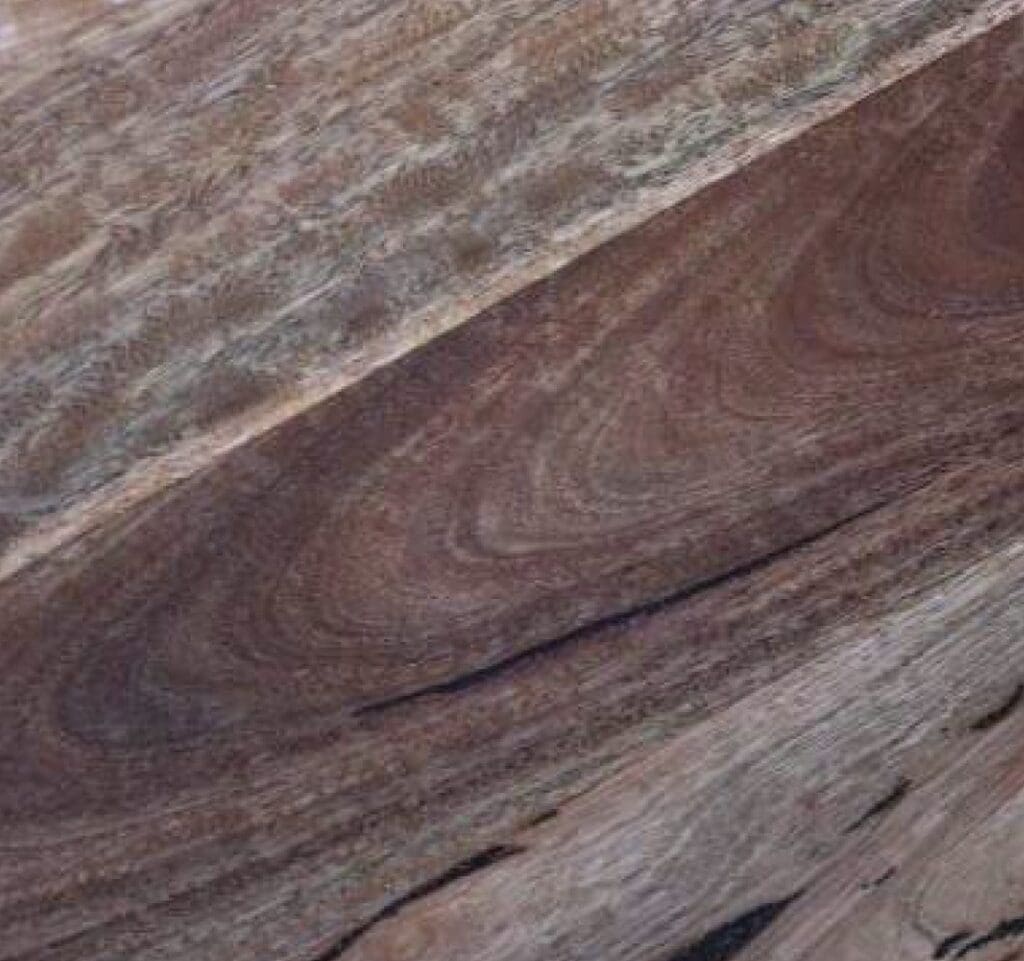
The photo to the left shows circular swirl marks that are visible under down light. The photo to the right shows the same section of floor in natural light without the down ights on and the swirl marks are not visible.
- Delamination – Separation of one coating from another or from the coating to the board should not generally occur in a floor and in such instances remedial work is necessary. Minor delamination due to movement at board joints or ends can occur and provided it does not progress, remedial work is unlikely to be necessary.
- Gloss variation – Differing conditions in the dwelling at the time of curing can result in gloss variation. Although consistency can be expected at the time of a particular application, some variation may be apparent between areas when finished at a different time. Gloss variation within a room particularly with satin finishes usually requires remedial work.
- White lining – When gaps appear at board edges the stretching of the bridged coating can cause a white line to appear at board joints. Unless severe this conditions requires no remedial work.
- Lap and roller marks – Some finish systems are more prone than others and should lap or roller marks occur, they need to be minimal in number and not able to be observed from all directions, to be acceptable.
- Edge bonding – Some finish systems can act as an adhesive and bond board edges together. With shrinkage in the floor, wide irregular spaced gapping and splits in boards can occur. Only minor edge- bonding resulting in small gaps at board edges is acceptable. Frequent splits and wide gaps are not acceptable.
- Ghosting – Lighter toned boot and foot prints can occur in floors 6 to 18 months after the floor has been finished. In most instances the source of the mark cannot be identified and in most instances not likely to be associated with the sander and finisher. Re-sanding and finishing may correct the problem and a compromise between parties is often necessary to resolve the problem.
Colour changes to timber and coating
Over the course of time colour changes occur in timber floors from the effects of ultra violet light. Therefore, it is usually more pronounced in sun exposed areas of the floor. This is partly associated with the changes in the timber and partly with the coating that is applied. Some coatings darken with time more than others and some timbers are more prone to colour changes than others. This process is natural and often gradual but can result in distinct colour differences where rugs have been put on the floor.
Some of this change can be minimised by not putting rugs down till six or so months after the floor has been completed. It is beneficial for flooring contractors to make clients aware of how the coating used may result in colour differences. From there it is up to the owner to manage how rugs are used.
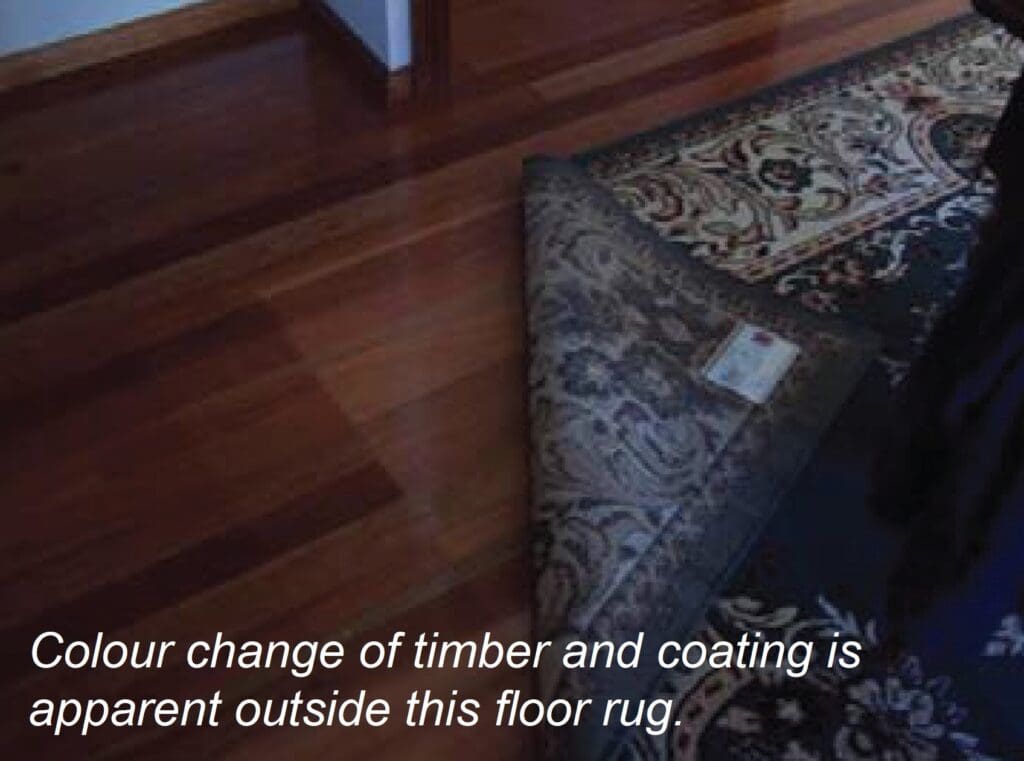